PLC là gì? Cách chọn PLC chuẩn tương thích cho quy trình tự động
PLC (Programmable Logic Controller – bộ điều khiển logic khả trình) là một thiết bị máy tính phục vụ trong lĩnh vực tự động hóa công nghiệp, giúp giám sát trạng thái dữ liệu đầu vào (input) và đầu ra (output), từ đó thực thi trình tự quyết định logic cho các quy trình hoặc máy móc tự động.
Nguyên lý hoạt động của PLC
PLC là một giải pháp điều khiển linh hoạt và mạnh mẽ, có thể thích nghi với hầu hết mọi ứng dụng. Bộ điều khiển sẽ nhận thông tin từ các cảm biến hoặc thiết bị input được kết nối, sau đó xử lý dữ liệu và kích hoạt hành động output dựa trên các tham số được lập trình sẵn.
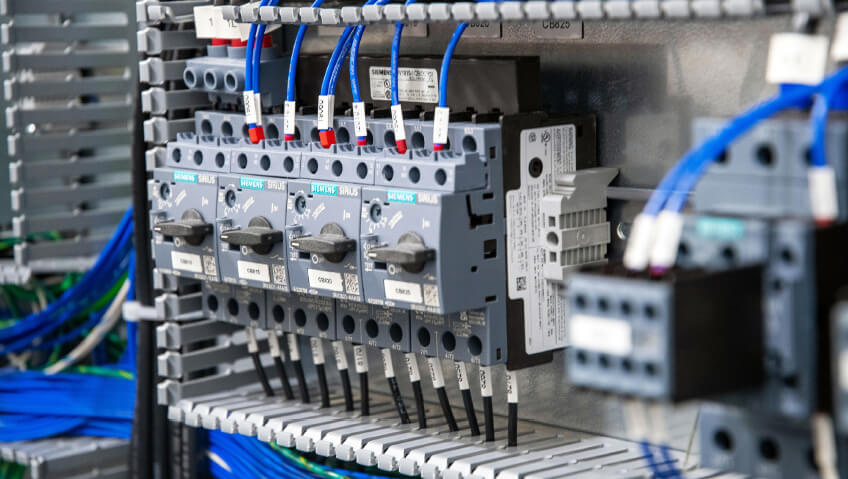
Tùy thuộc vào input và output, PLC sẽ theo dõi và ghi lại dữ liệu quy trình thực thi về năng suất máy hoặc nhiệt độ vận hành, tự động khởi động và dừng quy trình, tạo báo động khi máy hỏng hóc, v.v.
Dưới đây là một số đặc trưng giúp phân biệt PLC với máy tính công nghiệp, bộ vi điều khiển hoặc các giải pháp kiểm soát tự động hóa công nghiệp khác:
Cơ chế I/O (Input/Output)
CPU của PLC lưu trữ và xử lý dữ liệu lập trình, nhưng mô-đun input và ouput mới là nhân tố giúp kết nối PLC với phần còn lại của hệ thống máy móc. Các mô-đun I/O này cung cấp thông tin cho CPU và kích hoạt các kết quả tương ứng.
Doanh nghiệp có thể lựa chọn I/O theo định dạng analog hoặc digital. Thiết bị input bao gồm cảm biến, công tắc và đồng hồ đo; thiết bị output là rơ-le, đèn, van, ổ đĩa cứng… Các yếu tố I/O có thể được phối hợp và cài đặt linh hoạt theo ý muốn để đạt được cấu hình phù hợp cho mục đích của doanh nghiệp.
Giao thức kết nối
Ngoài các thiết bị đầu vào và đầu ra, PLC cũng cần kết nối với các loại hệ thống khác.
Ví dụ, doanh nghiệp có thể tìm cách xuất dữ liệu ứng dụng PLC tới hệ thống giám sát và thu thập dữ liệu (SCADA). Tin tốt là PLC hỗ trợ tương thích với nhiều lơaj chọn cổng và giao thức kết nối, đảm bảo giao tiếp hiệu quả lẫn nhau.
Giao diện người-máy (HMI)
Để tương tác với PLC theo thời gian thực, người dùng cần tích hợp HMI – có thể theo định dạng màn hình đơn giản, hiển thị văn bản và giao diện bàn phím, hoặc các bảng điều khiển cảm ứng. Dù bằng cách nào, chúng vẫn cần thỏa mãn nhu cầu kiểm tra và nhập liệu thông tin cho PLC.
Vai trò của từng yếu tố cấu thành nên PLC
Input
PLC ghi nhận các dữ liệu đầu vào liên quan và gửi đến CPU. Một số PLC chỉ dùng dữ liệu input theo định dạng on/off, nhưng các loại PLC analog lại có thể nhận dữ liệu biến thiên đa dạng hơn. Rất nhiều loại thiết bị có thể được sử dụng để cung cấp input, như hệ thống IoT, robot, cảm biến an toàn, giao diện người-máy…
Logic lập trình
Mỗi PLC được thiết kế với một bộ vi xử lý CPU (16 bit hoặc 32 bit). Kỹ sư lập trình CPU sẽ giúp PLC nhận biết các điều kiện và giá trị nhất định, kiểm tra trạng thái các biến số, sau đó lựa chọn câu lệnh thực thi đầu ra dựa trên các quy tắc được lập trình sẵn.
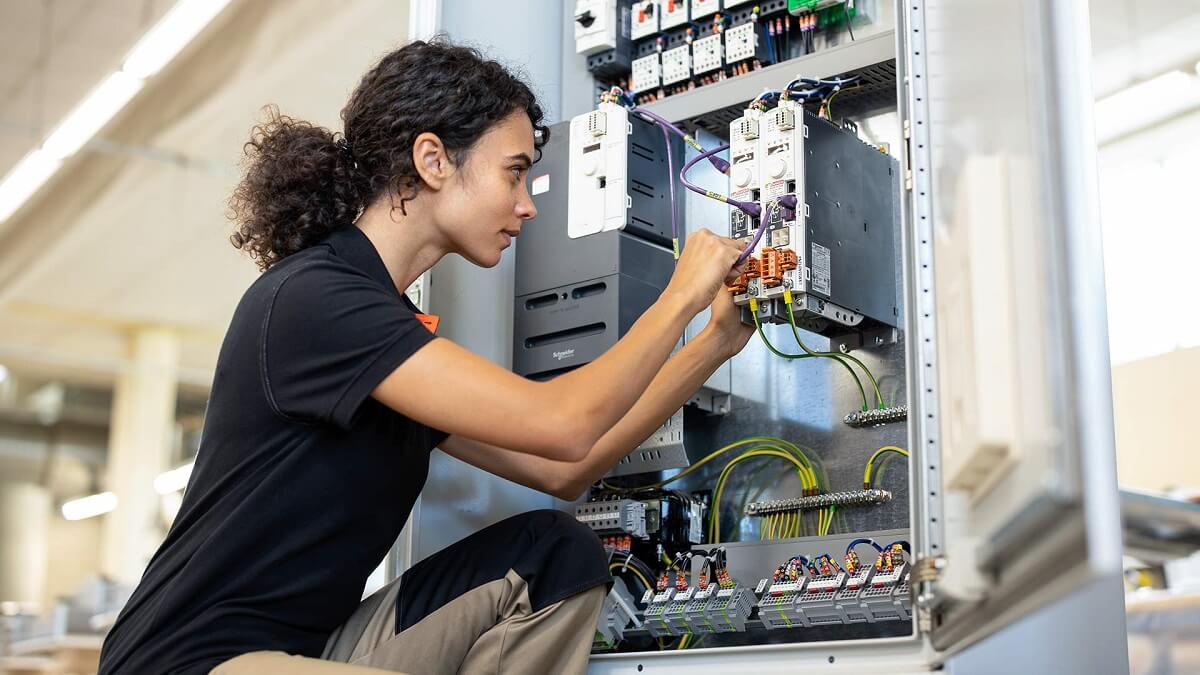
Output
Dựa trên logic lập trình, PLC sẽ điều khiển các công tắc, bộ khởi động, rơ-le và các thiết bị khác kết nối với đầu ra. Đây cũng là cơ chế cốt lõi cho phép PLC kiểm soát các quy trình vận hành máy móc. Đối với hệ thống lớn, các kỹ sư cũng có thể liên kết nhiều bộ phận bằng cách lập trình PLC để gửi tín hiệu đầu ra tới một PLC khác trong cùng chuỗi quy trình.
Phân biệt 2 loại PLC phổ biến
Compact PLC (PLC nhỏ gọn)
Conpact PLC có input và output tích hợp trực tiếp trên chính vi điều khiển. Cấu tạo input và output đều cố định, nên Compact PLC không có khả năng mở rộng mô-đun linh hoạt.
Modular PLC (PLC mô-đun)
Một Modular PLC thường có thiết kế phù hợp để lắp đặt nhiều mô-đun, cho phép mở rộng hệ thống nhiều lần và bổ sung thêm lựa chọn tính năng như tăng số lượng đơn vị I/O.
PLC mô-đun thường dễ sử dụng hơn vì mỗi thành phần vận hành độc lập với nhau, đồng nghĩa với việc nhân sự phụ trách có thể khắc phục sự cố nhờ cách ly các mô-đun để xử lý.
Ngoài ra, Modular PLC cũng thường có nguồn điện và mô-đun giao thức kết nối riêng. Do đó, PLC mô-đun thường hỗ trợ tính năng linh hoạt hơn so với PLC nhỏ gọn.
Những yếu tố quan trọng được ưu tiên khi chọn PLC bao gồm: khả năng mở rộng, số lượng I/O, phát hiện lỗi, thời gian ngừng hoạt động, kết hợp mô-đun và bộ nhớ. Do vậy, giữa 2 loại trên, PLC mô-đun thường được ưu tiên nhiều hơn, đặc biệt đối với các hệ thống công nghiệp lớn yêu cầu nhiều thiết bị với I/O cần được điều khiển chặt chẽ.
Lợi ích & ứng dụng của PLC
- Dễ lập trình: Ngôn ngữ lập trình của PLC đơn giản hơn so với các hệ thống điều khiển công nghiệp khác, khiến chúng trở thành mộ trong những lựa chọn tối ưu cho các doanh nghiệp muốn giảm thiểu chu phí và độ phức tạp.
- Công nghệ hoàn thiện: PLC là một sáng chế đã qua nhiều năm thử nghiệm và phân tích, hỗ trợ tìm kiếm và tra cứu thông tin hướng dẫn lập trình và tích hợp cho nhiều định dạng PLC khác nhau.
- Chi phí linh hoạt: PLC phục vụ nhu cầu chi phí đa dạng, gồm nhiều mẫu cơ bản cực kỳ rẻ mà các doanh nghiệp nhỏ và công ty khởi nghiệp thường sử dụng.
- Chức năng phong phú: Trong hầu hết mọi trường hợp, doanh nghiệp sẽ luôn tìm thấy mẫu PLC tương thích để điều khiển quy trình và hệ thống.
- Chất lượng bền bỉ: Thiết kế của PLC không bao gồm các bộ phận chuyển động, khiến chúng hoạt động ổn định lâu dài và ít ảnh hưởng bởi hao mòn tự nhiên trong nhiều điều kiện công nghiệp khắc nghiệt.
- Dễ sửa chữa: PLC được cấu thành bởi rất ít thành phần, càng khiến công sức xử lý và khắc phục sự cố nhanh hơn, giảm thời gian ngưng trệ cho hoạt động bảo trì máy móc.
- Tiết kiệm năng lượng: Hoạt động của PLC tiêu thụ rất ít điện năng, giúp cắt bớt chi phí và nỗ lực đầu tư cho việc thiết lập hệ thống vật lý.
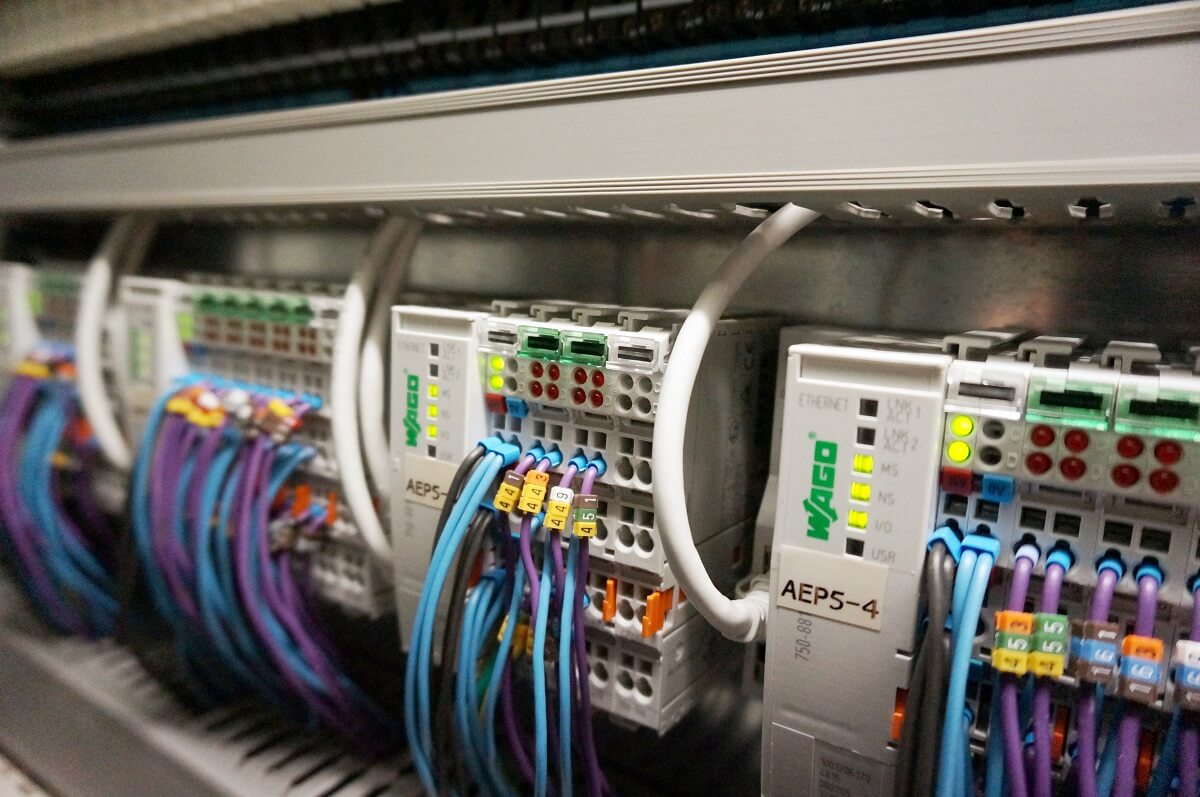
Nhược điểm của PLC
Không có công nghệ nào hoàn hảo 100%, nên PLC đôi khi chưa phải lựa chọn tối ưu trong một số bối cảnh.
- PLC không xử lý hiệu quả các dữ liệu quy trình có độ phức tạp cao. Do đó, khi doanh nghiệp sản xuất mở rộng quy mô tích hợp công nghệ, lựa chọn hợp lý hơn sẽ là các hệ thống điều khiển phân tán (DCS) hoặc phương pháp quản lý công nghiệp khác.
- PLC của các nhà sản xuất khác nhau thường sử dụng phần mềm lập trình độc quyền. Điều này khiến việc kết nối giao diện lập trình giữa nhiều PLC có thể gặp vấn đề cản trở nhất định.
- Giống như nhiều loại thiết bị điện tử khác, PLC dễ bị nhiễu điện từ, hoặc gặp các loại trục trặc điện tử thông thường khác, như bộ nhớ bị hỏng, lỗi giao tiếp…
Tiêu chuẩn để chọn PLC cho quy trình doanh nghiệp
Có rất nhiều yếu tố ảnh hưởng đến lựa chọn PLC khi áp dụng vào quy trình doanh nghiệp. Một số những yếu tố quan trọng nhất bao gồm:
- Công suất điện: Tùy PLC mà yêu cầu điện áp khác nhau; hãy kiểm tra để đảm bảo phù hợp với thông số hệ thống nguồn điện đang sử dụng.
- Tốc độ xử lý: Kiểm tra tốc độ CPU của PLC để xác định khả năng đáp ứng được nhu cầu ứng dụng PLC vào hệ thống.
- Khả năng tương thích: Đảm bảo rằng PLC hoạt động tương thích với bất kỳ phần cứng hệ thống mới hoặc hiện có nào.
- Khả năng chịu nhiệt: Hầu hết các PLC được thiết kế để hoạt động an toàn trong khoảng từ 0 – 60°C. Tuy nhiên, một số loại PLC chuyên dụng có thể vận hành ở mức nhiệt cực cao, cũng là lưu ý cần thiết cho các cơ sở công nghiệp có điều kiện sản xuất nóng/lạnh bất thường.
- Giới hạn bộ nhớ: PLC cần đủ ROM và RAM để thực thi các quy trình tự động hóa. ROM giúp bộ điều khiển lưu trữ hệ điều hành và các câu lệnh lập trình, còn RAM giúp thực thi chức năng một cách ổn định.
- Tình trạng kết nối: Đảm bảo PLC có đủ cổng input và output, đồng thời cho phép kết nối với loại thiết bị ngoại vi mà hệ thống doanh nghiệp yêu cầu.
- Đầu vào/đầu ra analog: Cân nhắc sử dụng PLC có cơ chế analog cho input và output để điều khiển được quy trình liên quan đến biến số dao động liên tục.