Chu trình PDCA là gì? 4 bước áp dụng PDCA để cải tiến sản xuất
Chu trình PDCA, hay chu trình Deming, là một phương pháp quản lý nhằm cải tiến quy trình liên tục, bổ trợ nền tảng lý thuyết ứng dụng phương pháp Kaizen trong sản xuất. PDCA được thiết kế dựa trên 4 giai đoạn: lập kế hoạch (Plan), thực hiện (Do), kiểm tra (Check), và hành động (Act).
Về bản chất, chu trình PDCA là một mô hình vòng lặp được thực hiện tuần tự theo từng bước, giúp các doanh nghiệp phát hiện, thực hiện, đánh giá và cải tiến liên tục. Mục tiêu cuối cùng của chu trình PDCA là cải thiện quy trình, ngăn ngừa các lỗi lặp lại và đảm bảo rằng mọi thay đổi được thực hiện đều hiệu quả và bền vững.
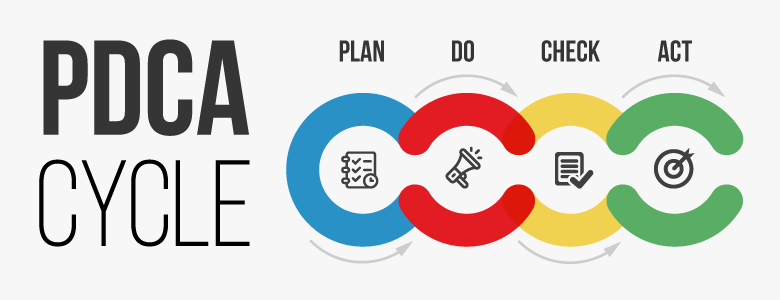
Lịch sử hình thành và phát triển chu trình PDCA
Chu trình PDCA ban đầu được phát triển vào những năm 1920 bởi Walter A. Shewhart, một nhà thống kê, nhà vật lý và kỹ sư người Mỹ. Chu trình Shewhart hướng đến quy trình sản xuất đáng tin cậy, tạo ra các sản phẩm chất lượng cao với tỷ lệ lỗi thấp hơn, bao gồm 3 bước: Xác định (Specify) – Sản xuất (Produce) – Kiểm tra (Inspect).
Về sau, tiến sĩ W. Edwards Deming đã phát triển chu trình Shewhart và mở rộng thành chu trình PDCA ngày nay. Chu trình PDCA – hay còn gọi là chu trình Deming – liên quan chặt chẽ đến khái niệm về chất lượng sản phẩm, đổi mới và học hỏi thông qua thực hành trong vòng đời của một sản phẩm.
4 bước quy trình áp dụng PDCA
Chu trình PDCA là một quy trình lặp đi lặp lại nhằm cải tiến liên tục sản phẩm, con người và dịch vụ, trở thành một phần không thể thiếu trong lĩnh vực sản xuất tinh gọn (lean manufacturing) ngày nay. Chu trình PDCA bao gồm 4 bước:
Bước 1: Lập kế hoạch (Plan)
Lập kế hoạch là bước đầu tiên trong chu trình PDCA, thường được chia thành các bước nhỏ nhằm xác định cụ thể những việc cần thực hiện, từ đó xây dựng một chiến lược hợp lý với ít rủi ro thất bại hơn. Tùy thuộc vào quy mô của dự án, việc lập kế hoạch có thể kéo dài hơn thời gian dự kiến và đòi hỏi nhiều nguồn lực hơn. Để thực hiện tốt quá trình lập kế hoạch, doanh nghiệp cần xem xét các yếu tố sau:
- Vấn đề cốt lõi cần giải quyết
- Mục tiêu cần đạt được
- Các nguồn lực cần thiết
- Thời gian dự kiến hoàn thành dự án
- Các bên liên quan cần được tham gia
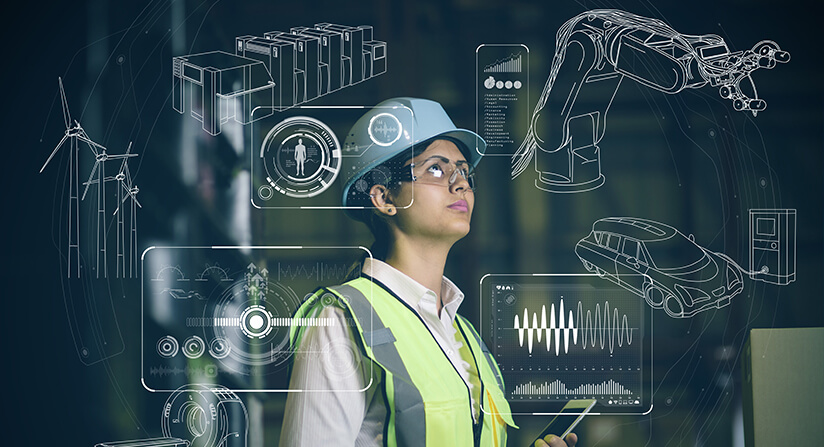
Bước 2: Thực hiện (Do)
Sau khi hoàn thành việc lập kế hoạch cụ thể, doanh nghiệp có thể tiến đến bước thực hiện và triển khai kế hoạch trong thực tế. Tuy nhiên, trước khi triển khai một cách toàn diện, doanh nghiệp cần thử nghiệm kế hoạch trên quy mô nhỏ để đánh giá tính khả thi, giảm rủi ro và phát hiện sớm các vấn đề tiềm ẩn.
Đồng thời, trong suốt quá trình thử nghiệm, doanh nghiệp có thể ghi chép lại các dữ liệu và thông tin quan trọng làm cơ sở cho việc đánh giá và triển khai kế hoạch trên thực tiễn ở các bước sau.
Khi thử nghiệm thành công, doanh nghiệp có thể tiến hành chuẩn hóa quy trình để đảm bảo mọi hoạt động được thực hiện một cách đồng bộ và nhất quán khi mở rộng quy mô. Tuy nhiên, trong giai đoạn này vẫn có thể phát sinh những vấn đề không lường trước, vì vậy việc chuẩn bị sẵn sàng các biện pháp ứng phó là vô cùng cần thiết.
Bước 3: Kiểm tra (Check)
Kiểm tra là bước vô cùng quan trọng trong chu trình PDCA nhằm đảm bảo mọi thứ diễn ra suôn sẻ và theo đúng kế hoạch. Trong giai đoạn “Kiểm tra” của chu trình PDCA, doanh nghiệp thu thập và đánh giá kết quả từ những thử nghiệm nhỏ của mình. Nếu thử nghiệm chứng minh thành công, doanh nghiệp sẽ triển khai thay đổi trên quy mô rộng hơn. Ngược lại, nếu không thành công, doanh nghiệp cần phân tích nguyên nhân, xác định các vấn đề còn tồn đọng để đưa ra hướng giải quyết phù hợp.
Bước 4: Hành động (Act)
Bước cuối cùng trong chu trình PDCA là Hành động, tại đây doanh nghiệp có thể dựa trên những phân tích, đánh giá ở bước 3 và đưa ra hành động phù hợp. Cụ thể, nếu kế hoạch thử nghiệm ở quy mô nhỏ đạt hiệu quả cao, doanh nghiệp có thể triển khai trên quy mô lớn hơn.
Ngược lại, nếu các cải tiến chưa đạt yêu cầu, doanh nghiệp cần quay lại bước đầu tiên – lập kế hoạch – để thử nghiệm một giải pháp khác và tiến hành lại tuần tự các bước trong chu trình PDCA. Thông qua đó, doanh nghiệp có thể đảm bảo rằng các cải tiến được triển khai một cách đồng bộ, tạo ra một nền tảng vững chắc cho các hoạt động trong tương lai.
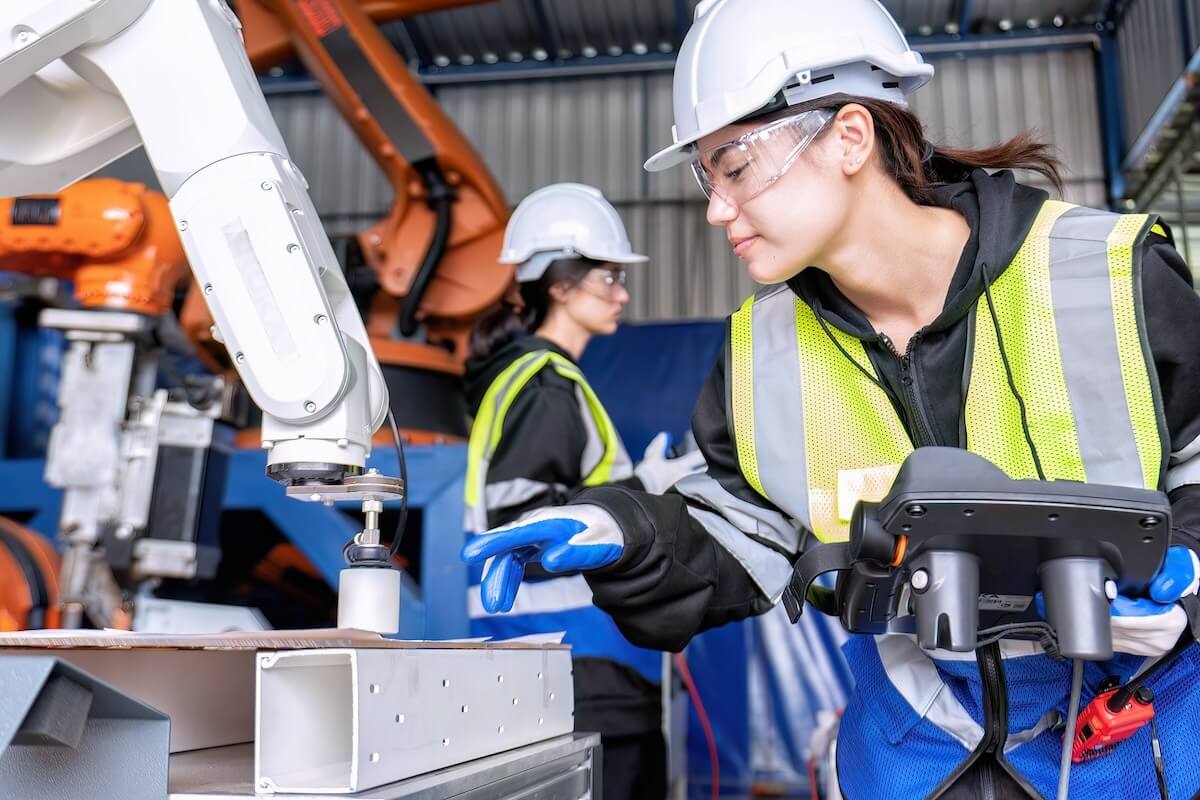
Ưu điểm & nhược điểm của chu trình PDCA
Ưu điểm
- Tối ưu hóa nguồn lực: Giảm thiểu lãng phí, tiết kiệm chi phí và nâng cao hiệu quả hoạt động
- Giải quyết vấn đề hiệu quả: Xác định nguyên nhân gốc rễ của các yếu tố không hiệu quả và nhanh chóng triển khai các giải pháp khắc phục
- Tính linh hoạt: Khả năng thích ứng với sự thay đổi để đẩy nhanh quá trình giải quyết vấn đề
- Nâng cao chất lượng: Giảm thiểu sai sót và rủi ro trong quy trình, tạo ra sản phẩm và dịch vụ với chất lượng cao
- Thúc đẩy sự phát triển của doanh nghiệp: Cải tiến liên tục quy trình giúp gia tăng sự hài lòng của khách hàng, từ đó thúc đẩy sự phát triển của doanh nghiệp.
Nhược điểm
- Đòi hỏi đầu tư thời gian và nguồn lực: Việc thực hiện và lặp lại chu trình PDCA tốn khá nhiều thời gian, đòi hỏi doanh nghiệp cần kiên trì, nỗ lực học hỏi và cải tiến liên tục để đạt hiệu quả tối ưu.
- Không phù hợp với các dự án khẩn cấp: PDCA là một phương pháp cải tiến liên tục và được thực hiện lặp đi lặp lại trong một thời gian dài đến khi đạt kết quả như ý, vì vậy chu trình này không hiệu quả với các dự án cấp thiết và yêu cầu cần có giải pháp ngay lập tức.
ĐỌC THÊM:
- 5S là gì trong sản xuất? Cách áp dụng 5S & lợi ích cho doanh nghiệp
- Quy tắc 4M là gì trong sản xuất? Cách áp dụng & cải tiến 4M hiệu quả
- Phương pháp Kaizen là gì? 5 bước triển khai Kaizen trong sản xuất
Cách triển khai chu trình PDCA để giảm lãng phí trong sản xuất tinh gọn
Giai đoạn 1: Lập kế hoạch – Xác định lãng phí
Trong giai đoạn Lập kế hoạch (Plan), doanh nghiệp sẽ lập sơ đồ quy trình hiện tại, thu thập dữ liệu và phân tích nguồn gốc phát sinh lãng phí, sử dụng sơ đồ dòng giá trị, nghiên cứu thời gian, hoặc sơ đồ spaghetti nhằm làm nổi bật các điểm không hiệu quả như di chuyển quá nhiều, xử lý thừa, hoặc tắc nghẽn. Khi lãng phí được nhận diện, doanh nghiệp sẽ bắt đầu xây dựng chiến lược để loại bỏ hoặc giảm thiểu nó.
Để định lượng tác động của lãng phí và hiểu rõ hơn các điểm cần cải thiện, doanh nghiệp có thể sử dụng các công cụ chuyên dụng như Orca Lean Waste Calculator – máy tính tính toán lãng phí – giúp cung cấp đánh giá cụ thể về ảnh hưởng của từng loại lãng phí đối với hiệu suất và chi phí tổng thể.
Giai đoạn 2: Thực hiện – Thử nghiệm việc giảm lãng phí
Giai đoạn Thực hiện (Do) tập trung vào triển khai giải pháp đã lên kế hoạch trên quy mô nhỏ, qua đó, doanh nghiệp có thể kiểm tra tính hiệu quả của thay đổi đề xuất mà không làm gián đoạn quy trình chung.
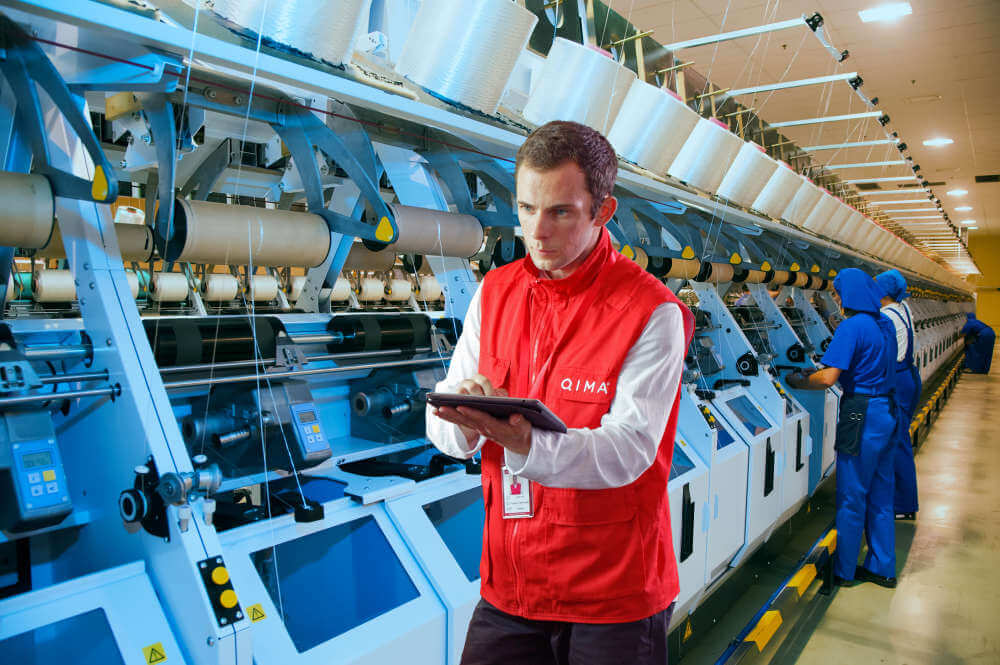
Doanh nghiệp có thể tích hợp các công cụ lean như phương pháp 5S (Sàng lọc, Sắp xếp, Làm sạch, Chuẩn hóa, Duy trì) và SMED (Single Minute Exchange of Die). Ví dụ, áp dụng 5S có thể giúp giảm thiểu di chuyển không cần thiết bằng cách tổ chức lại không gian làm việc hợp lý hơn.
Giai đoạn 3: Kiểm tra – Giám sát kết quả
Giai đoạn Kiểm tra (Check) là lúc doanh nghiệp đánh giá lại kết quả của thay đổi đã thực hiện. Bằng cách đo lường các chỉ số hiệu suất chính (KPI) như thời gian chu kỳ, mức tồn kho, hoặc tỷ lệ lỗi, doanh nghiệp có thể xác định liệu giải pháp có thực sự giảm lãng phí hiệu quả hay không. Phương pháp sản xuất tinh gọn đặc biệt chú trọng quản lý trực quan, giúp so sánh dễ dàng giữa kết quả trước và sau.
Giai đoạn 4: Hành động – Chuẩn hóa quy trình
Trong giai đoạn Hành động (Act), doanh nghiệp tiến hành phản ánh kết quả thử nghiệm, đánh giá tính hiệu quả của các giải pháp đã đề ra trong kế hoạch dựa trên quá trình thử nghiệm. Nếu kết quả thử nghiệm cho thấy giải pháp đã giảm lãng phí hiệu quả, quy trình có thể được chuẩn hóa và triển khai toàn bộ tổ chức.
Ngược lại, nếu giải pháp không mang lại hiệu quả cao như mong đợi, doanh nghiệp sẽ bắt đầu lại từ đầu, từ việc tinh chỉnh kế hoạch và lặp lại chu trình PDCA cho đến khi đạt được kết quả mong muốn. Khi quy trình đã được chuẩn hóa, doanh nghiệp sẽ tiếp tục theo dõi để tìm thêm các cơ hội cải tiến, đảm bảo lãng phí luôn ở mức tối thiểu.