5S là gì trong sản xuất? Cách áp dụng 5S & lợi ích cho doanh nghiệp
Phương pháp 5S là quy trình chuẩn hóa nhằm thiết lập và duy trì các tiêu chuẩn làm việc an toàn, sạch sẽ và hiệu quả, bao gồm biện pháp kiểm soát trực quan giúp phát hiện và khắc phục nhanh chóng sai sót trong quy trình sản xuất. 5S cũng là một phần không thể thiếu trong trường phái lean manufacturing (sản xuất tinh gọn).
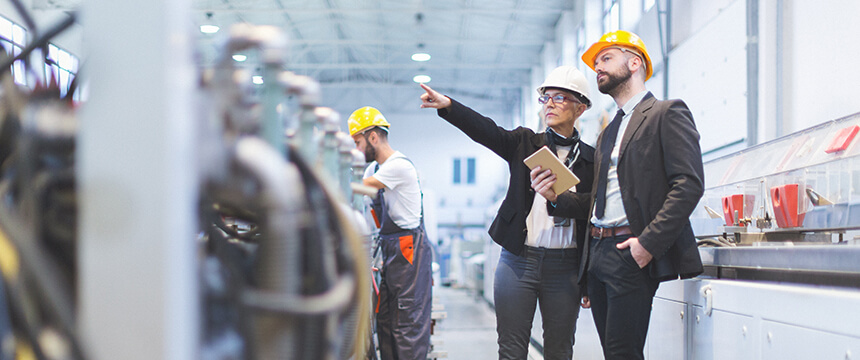
Tại sao 5S trong sản xuất lại quan trọng?
Mặc dù bắt nguồn từ ngành công nghiệp ô tô nhưng hiện nay 5S đã được áp dụng rộng rãi ở nhiều lĩnh vực khác, nhờ hiệu quả chứng minh đem lại rất nhiều lợi ích trong cả việc tổ chức lẫn loại bỏ lãng phí. Ngoài ra, 5S cũng đóng vai trò nền tảng cốt lõi của hệ thống phương pháp bảo trì năng suất toàn diện (TPM), triết lý hệ thống sản xuất Toyota (TPS), cũng như phương pháp Kaizen (cải tiến liên tục).
Giải nghĩa trình tự 5S
5S bao gồm các bước sau :
- Seiri (Sàng lọc): Loại bỏ vật dụng không cần thiết.
- Seiton (Sắp xếp): Sắp xếp các vật dụng cần thiết vào đúng vị trí.
- Seiso (Làm sạch): Dọn sạch nơi làm việc và thiết bị.
- Seiketsu (Chuẩn hóa): Thiết lập quy trình duy trì 5S.
- Shitsuke (Duy trì): Đảm bảo việc thực hiện 5S thường xuyên và hiệu quả.
Mỗi bước trong quy trình 5S được liên kết chặt chẽ với nhau để tạo ra chu trình 5S toàn diện nên thứ tự trên cần được đảm bảo cố định.
Chẳng hạn, việc loại bỏ những vật liệu không cần thiết trong bước 1 (Sàng lọc) sẽ tạo ra không gian cần thiết để sắp xếp những vật phẩm quan trọng trong bước 2 (Sắp xếp). Khi không gian làm việc đã được dọn dẹp ngăn nắp, bụi bẩn và các chất thải sẽ được loại bỏ trong bước 3 (Làm sạch).
Những thay đổi đối với môi trường làm việc của nhân viên cần được phản ánh thông qua quy trình cập nhật ở bước 4 (Chuẩn hóa). Cuối cùng, nhân sự phân công trách nhiệm rõ ràng và theo dõi tiến độ – như được yêu cầu trong bước 5 (Duy trì).
Xong xuôi, nhân viên sẽ tiếp tục tuần tự áp dụng từng bước trong phương pháp 5S, quay lại bước đầu tiên để duy trì và cải thiện liên tục.
Khái niệm chi tiết từng bước quy trình 5S
Seiri (Sàng lọc)
Trong bước Sàng lọc, những thứ không cần thiết sẽ được phân loại để chuyển sang đánh giá và xử lý. Thông thường, các vật dụng này sẽ được phân loại theo 4 nhóm:
- Vật dụng cần thiết cho khu vực hiện tại.
- Vật dụng thuộc khu vực khác.
- Vật dụng có thể cần trong tương lai gần (gắn thẻ đỏ).
- Vật dụng không cần thiết (loại bỏ hoặc tái chế).
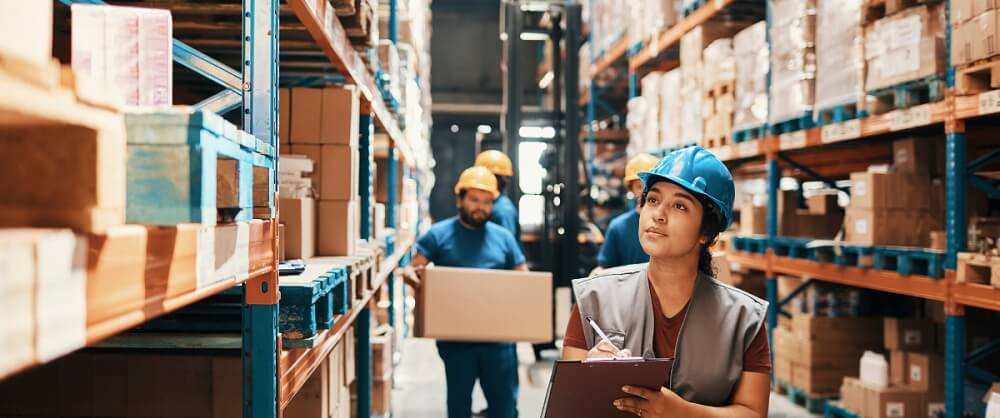
Seiton (Sắp xếp)
Ở bước Sắp xếp, các vật dụng được tái tổ chức vị trí để trở nên dễ tìm, nhằm giảm thời gian tìm kiếm và tăng hiệu quả công việc. Seiton bao gồm các thao tác:
- Đặt vật dụng thường dùng trong tầm với.
- Xếp chung các vật dụng tương tự với nhau.
- Sử dụng nhãn dán và bảng hiệu để nhận biết nhanh chóng vị trí từng vật.
- Tổ chức đánh giá định kỳ để cải thiện cách sắp xếp.
Seiso (Làm sạch)
Bước Làm sạch sẽ đảm bảo nhiệm vụ vệ sinh và bảo trì thiết bị để phát hiện và ngăn ngừa hư hỏng.
Seiso bao gồm các bước:
- Sử dụng công cụ và hóa chất phù hợp để vệ sinh.
- Kiểm tra và bảo dưỡng thiết bị sau khi làm sạch.
- Phát hiện và khắc phục kịp thời sự cố như rò rỉ hoặc hư hỏng.
Seiketsu (Chuẩn hóa)
Trong bước Chuẩn hoá, việc thiết lập các quy trình chuẩn để đảm bảo 5S được duy trì liên tục là vô cùng cần thiết, trong đó bao gồm:
- Ghi lại quy trình và tạo danh sách kiểm tra cho từng hoạt động.
- Đào tạo nhân viên để đảm bảo quy trình được thực hiện đúng.
- Tổ chức các buổi đánh giá định kỳ để cải thiện quy trình.
Shitsuke (Duy trì)
Cuối cùng, bước Duy trì sẽ củng cố lịch trình thực hiện 5S liên tục và cải tiến thường xuyên trong doanh nghiệp. Cách thực hiện như sau:
- Lên lịch thực hiện 5S theo tần suất cố định (hàng ngày, hàng tuần, hàng tháng).
- Giám sát và cung cấp phản hồi khi cần thiết.
- Khuyến khích nhân viên đóng góp ý kiến để cải thiện quy trình.
Quy trình áp dụng 5S vào doanh nghiệp sản xuất
Bước 1: Lên kế hoạch
Trước khi bắt tay vào triển khai 5S, đội ngũ lãnh đạo doanh nghiệp cần tổ chức họp mặt và thảo luận nhằm xây dựng một kế hoạch nhất quán, đảm bảo trình tự diễn ra hợp lý, bởi thay đổi này có ý nghĩa to lớn trên quy mô tổng thể.
Bước 2: Đào tạo, hướng dẫn thực hiện
Mỗi kế hoạch thôi chưa đủ, mà doanh nghiệp cần làm rõ vai trò của từng nhân sự đóng góp vào quá trình thực hiện theo dự định đặt ra.
Cụ thể, thông tin về tiêu chuẩn 5S, những ý nghĩa và giá trị tiềm năng mang lại cần được phổ biến rõ ràng cho nhân viên. Việc này giúp tập thể nhân công nhận thức được rõ tính quan trọng của kế hoạch, đồng thời củng cố tinh thần nghiêm túc khi phối hợp triển khai.
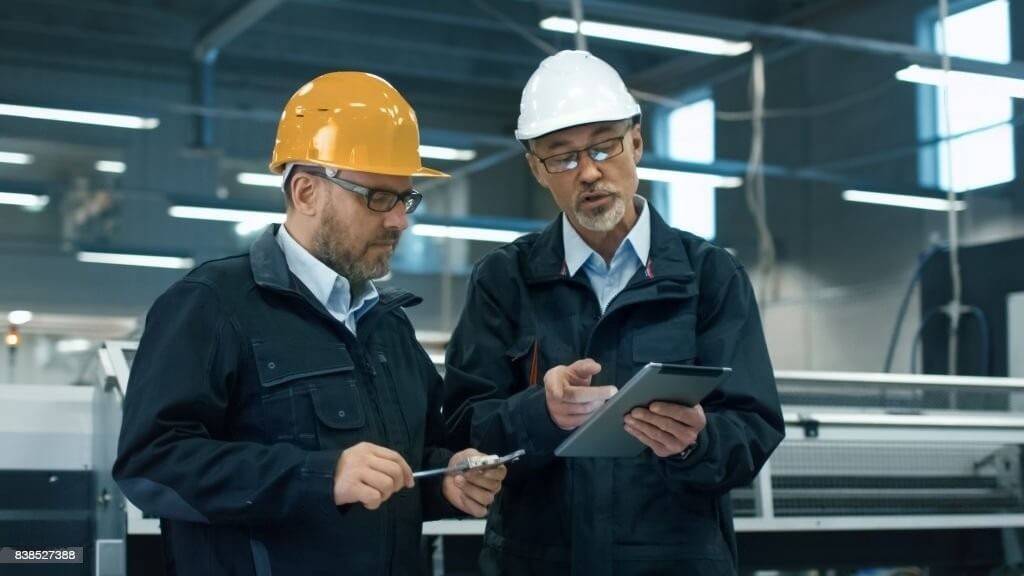
Để tăng cường mức độ ủng hộ và hạn chế tinh thần đối phó, các cấp quản lý có thể tiến hành khảo sát ý kiến và phản ứng của tập thể, từ đó áp dụng điều chỉnh phù hợp để đi đến quan điểm đồng thuận thống nhất.
Bước 3: Tiến hành thực hiện quy trình 5S
- Seiri: Loại bỏ vật dụng không cần thiết, giữ lại các vật dụng quan trọng.
- Seiton: Sắp xếp các vật dụng cần thiết theo vai trò và vị trí thuận tiện, kèm ghi chú rõ ràng.
- Seiso: Chủ động vệ sinh sạch sẽ không gian làm việc và các dụng cụ thường xuyên.
- Seiketsu: Đảm bảo tập thể thực hiện đúng và liên tục các bước Seiri, Seiton và Seiso.
- Shitsuke: Củng cố nhận thức cho tổ chức hiểu rõ lợi ích, mục đích của việc áp dụng quy trình 5S, từ đó tự giác áp dụng 5S mọi lúc mọi nơi.
Bước 4: Đánh giá và cải tiến quy trình
Sau khi triển khai phương pháp 5S trong sản xuất, doanh nghiệp cần tiếp tục theo dõi và đánh giá kết quả để cải thiện chất lượng quy trình. Thông qua dữ liệu có sẵn, những mặt tốt nên được tuyên dương và phát huy, tận dụng là thước đo đối chiếu cho những lần sau. Thậm chí, nếu có cơ hội, doanh nghiệp có thể học hỏi từ các tổ chức bên ngoài để tìm kiếm cơ hội tối ưu quy trình hiện có.
Bước 5: Duy trì kế hoạch thực hiện
Duy trì áp dụng 5S liên tục là bước cuối cùng, nhưng không phải để kết thúc, mà là cánh cửa mở ra cả một chặng đường kiên trì về sau. Những lợi ích và thói quen có ích từ 5S cần được áp dụng trở thành một phần văn hóa doanh nghiệp, có vậy mới đem lại giá trị thực sự của kế hoạch triển khai 5S.
ĐỌC THÊM:
- Chu trình PDCA là gì? 4 bước áp dụng PDCA để cải tiến sản xuất
- Quy tắc 4M là gì trong sản xuất? Cách áp dụng & cải tiến 4M hiệu quả
- Phương pháp Kaizen là gì? 5 bước triển khai Kaizen trong sản xuất
Lợi ích của phương pháp 5S trong sản xuất
Tạo thêm không gian hiệu quả
Việc áp dụng bước Sàng lọc (Seiri) giúp loại bỏ các vật dụng không cần thiết, giải phóng không gian trong khu vực làm việc. Điều này tạo ra môi trường thông thoáng, cho phép tổ chức lại không gian một cách chiến lược hơn. Không gian mới có thể được tận dụng để lưu trữ các thiết bị quan trọng hơn hoặc mở rộng khu vực sản xuất.
Ngoài ra, khu vực làm việc gọn gàng giúp giảm thiểu nguy cơ tai nạn vì không có vật dụng thừa gây cản trở lối đi hoặc làm ảnh hưởng đến luồng công việc. Doanh nghiệp có thể thấy rõ tác động tích cực này khi không gian được tổ chức tốt hơn.
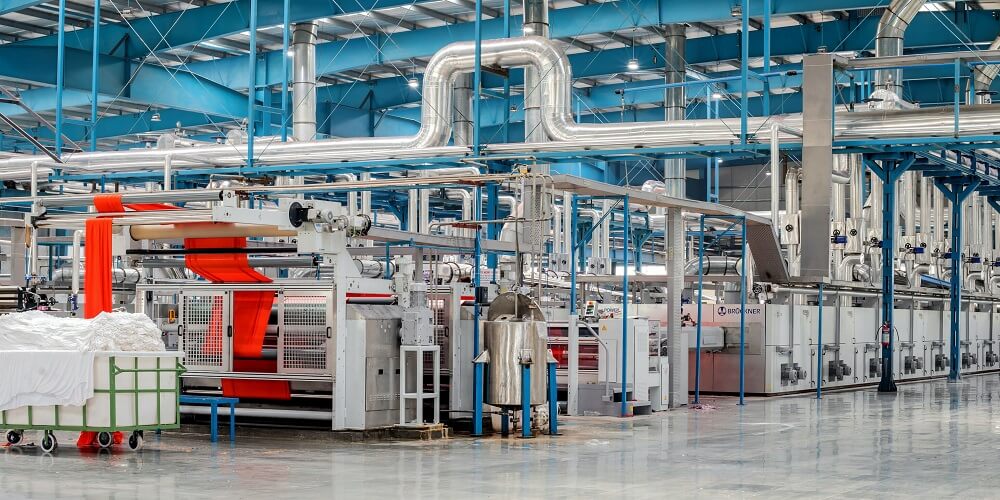
Giảm thời gian lãng phí và tăng năng suất
Trong bước Sắp xếp (Seiton), mọi công cụ và vật dụng cần thiết được đặt vào đúng vị trí dễ lấy, dễ trả lại. Nhờ đó, nhân viên không phải mất thời gian tìm kiếm vật dụng, giảm thiểu các thao tác không cần thiết trong quá trình làm việc.
Khi vật dụng thường dùng được đặt trong tầm với theo nguyên tắc công thái học, nhân viên có thể làm việc hiệu quả hơn và năng suất được tối ưu. Sự cải thiện về luồng công việc giúp tăng năng suất tổng thể, đồng thời giảm căng thẳng cho nhân viên khi mọi thứ đều sẵn sàng trong tầm tay và dễ sử dụng.
Cải thiện chất lượng và giảm downtime
Bước Làm Sạch (Seiso) không chỉ giúp duy trì môi trường làm việc gọn gàng mà còn cho phép nhân viên kiểm tra, bảo trì thiết bị thường xuyên. Việc phát hiện sớm các vấn đề như rò rỉ dầu, hao mòn hay hư hỏng thiết bị giúp ngăn ngừa sự cố gây gián đoạn sản xuất.
Bảo trì định kỳ đảm bảo thiết bị luôn trong tình trạng hoạt động tốt, giảm thiểu downtime (thời gian ngừng hoạt động) cũng như tăng độ tin cậy của quá trình sản xuất. Nhờ đó, doanh nghiệp có thể duy trì chất lượng sản phẩm ổn định và đáp ứng tiến độ giao hàng một cách nhất quán.
Khuyến khích nhân viên tham gia
Phương pháp 5S khuyến khích nhân viên góp sức chung để tổ chức và duy trì môi trường làm việc của bản thân. Khi có quyền kiểm soát khu vực làm việc thông qua việc thực hiện các bước 5S, nhân viên sẽ có tâm thế làm chủ và trở nên trách nhiệm hơn với công việc.
Đảm bảo an toàn và giảm thiểu rủi ro
Bằng cách loại bỏ các vật dụng không cần thiết và duy trì khu vực làm việc sạch sẽ, 5S giúp giảm nguy cơ xảy ra tai nạn trong môi trường làm việc. Những vật dụng không thật sự cần thiết không chỉ gây cản trở trong quá trình di chuyển mà còn có nguy cơ tiềm tàng trở thành mối nguy hiểm
Việc áp dụng các bước như vệ sinh và bảo dưỡng thiết bị thường xuyên giúp đảm bảo các công cụ và máy móc hoạt động ổn định, giảm thiểu rủi ro cho người lao động. Khi an toàn được đặt lên hàng đầu, nhân viên sẽ cảm thấy yên tâm và tập trung hơn vào công việc của mình.
Biến thể 6S (hay 5S+1)
Một số doanh nghiệp đã mở rộng phương pháp 5S bằng cách thêm yếu tố Safety để trở thành 6S (hoặc 5S+1) nhằm đảm bảo môi trường làm việc không chỉ gọn gàng, hiệu quả mà còn an toàn cho người lao động.
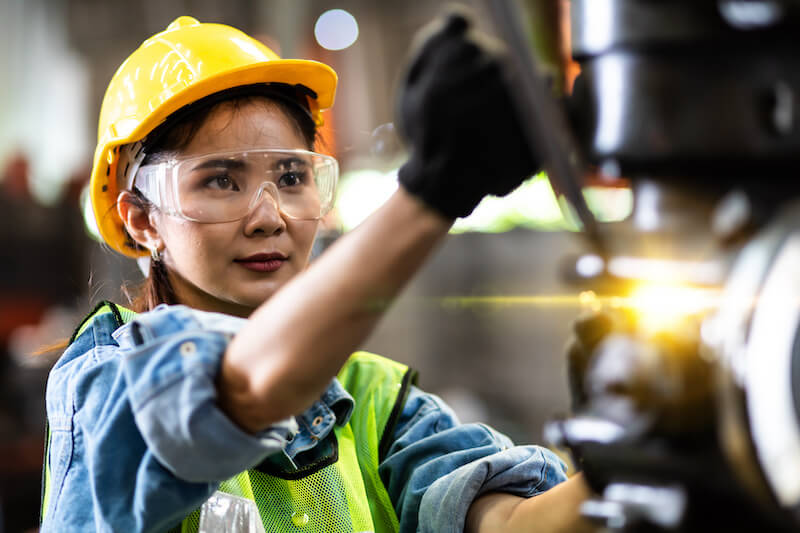
An toàn được xem như nguyên tắc nền tảng xuyên suốt mọi bước của quy trình bởi nơi làm việc sạch sẽ, được tổ chức tốt sẽ giảm thiểu các mối nguy tiềm ẩn, đồng thời bảo vệ sức khỏe và an toàn lao động của nhân viên.
Sự có mặt bổ sung của yếu tố Safety vào quy trình 5S không đơn thuần là phát hiện và loại bỏ các mối nguy – an toàn đã trở thành phần không thể thiếu trong văn hóa doanh nghiệp, thúc đẩy việc áp dụng các biện pháp bảo vệ sức khỏe và tạo điều kiện làm việc tốt nhất cho nhân viên.
Điều này đặc biệt cần thiết trong môi trường làm việc có tính rủi ro cao như nhà máy, công trường, hoặc kho bãi, nơi mà lỗi nhỏ cũng có thể dẫn đến tai nạn gây tử vong. Nhân viên làm việc trong môi trường an toàn cũng sẽ cảm thấy yên tâm hơn, từ đó tăng cường sự tập trung và hiệu quả công việc.