Poka Yoke là gì? 5 bước triển khai Poka-Yoke trong sản xuất
Poka Yoke là một thuật ngữ bắt nguồn từ Nhật Bản với ý nghĩa “chống sai sót”. Trong phạm vi sản xuất tinh gọn, poka-yoke là khái niệm đề cập đến các kỹ thuật được sử dụng để nhanh chóng xác định, sửa chữa hoặc ngăn chặn và phòng ngừa lỗi sai trong quá trình sản xuất.
Nói cách khác, poka-yoke được sinh ra để hoàn thiện các quy trình và sản phẩm theo chủ trương cầu toàn, phòng tránh hết mức khả năng xảy ra lỗi lầm và sai sót.
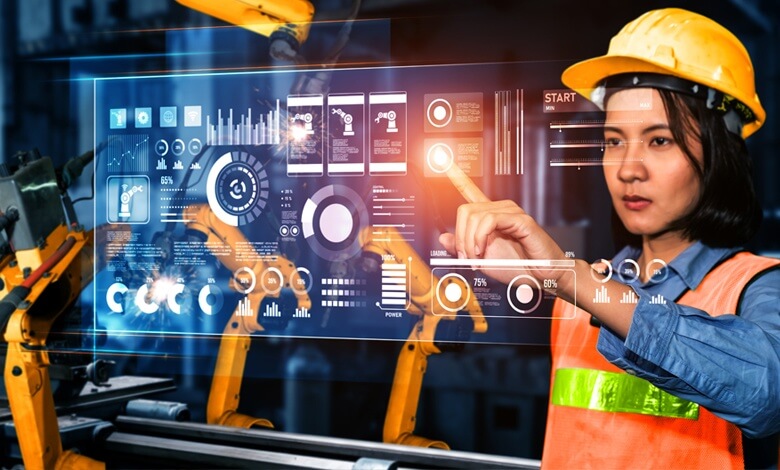
Phân loại các phương pháp Poka-Yoke
Tập hợp các loại hình phương pháp poka-yoke có thể chia thành 2 hướng áp dụng: Phòng ngừa lỗi và xác định/phát hiện lỗi.
1. Poka-yoke phòng ngừa lỗi
Phương pháp kiểm soát (control method)
Phương pháp kiểm soát có vai trò loại bỏ hoàn toàn xác suất khả thi khiến tình huống mắc lỗi xảy ra, giống như một chốt an toàn cuối cùng. Một số ví dụ đơn giản có thể thấy như chức năng kiểm tra chính tả cho văn bản soạn thảo, cơ chế ngăn tình trạng kẹt cửa thang máy khi có người bước vào, hoặc lò vi sóng tự động ngắt điện khi cửa chưa đóng kín.
Phương pháp cảnh báo (warning method)
Phương pháp cảnh báo sẽ nhắc nhở và phát ra tín hiệu/thông báo về khả năng xuất hiện lỗi, có thể thông qua âm thanh, màu sắc hoặc tin nhắn. Chẳng hạn, khi chuẩn bị xóa tập tin trên máy tính, một thông báo sẽ hiện lên để xác nhận lần cuối về quyết định chính xác của người dùng.
2. Poka-yoke phát hiện lỗi
Phương pháp tiếp xúc (contact method)
Poka-yoke xác định lỗi thông qua các thuộc tính tiếp xúc vật lý, thường sử dụng một thiết bị cảm biến để phát hiện những dấu hiệu bất thường về hình dạng, kích thước, màu sắc, trọng lượng sản phẩm – sau đó sẽ trả về kết quả kiểm tra cho người hoặc hệ thống phụ trách. Đây là cách thức được áp dụng phổ biến trong bối cảnh bị ảnh hưởng bởi những yếu tố dễ làm người lao động mất tập trung gây xảy ra lỗi.
Phương pháp giá trị cố định (fixed-value method)
Poka-yoke kiểm tra và đối chiếu số lượng hoặc tần suất chuyển động nhất định xảy ra trong quy trình có tính chất lặp lại. Phương pháp này thường áp dụng để theo dõi tần suất diễn ra của một tiến trình hoạt động và đảm bảo các tiêu chuẩn chất lượng được đáp ứng đầy đủ.
Ví dụ, một nhân viên chịu trách nhiệm lắp 6 ốc vít lên sản phẩm trước khi tiếp tục chuyển giao sang khâu tiếp theo, vậy giá trị cố định cần theo dõi cho quy trình này là 6 lần để đảm bảo công việc được hoàn thành. Khi áp dụng poka-yoke, doanh nghiệp có thể chuẩn bị sẵn các hộp chứa 6 ốc vít cố định, giúp nhân viên dễ dàng kiểm tra độ chính xác chỉ bằng việc sử dụng hết số ốc vít theo từng hộp.
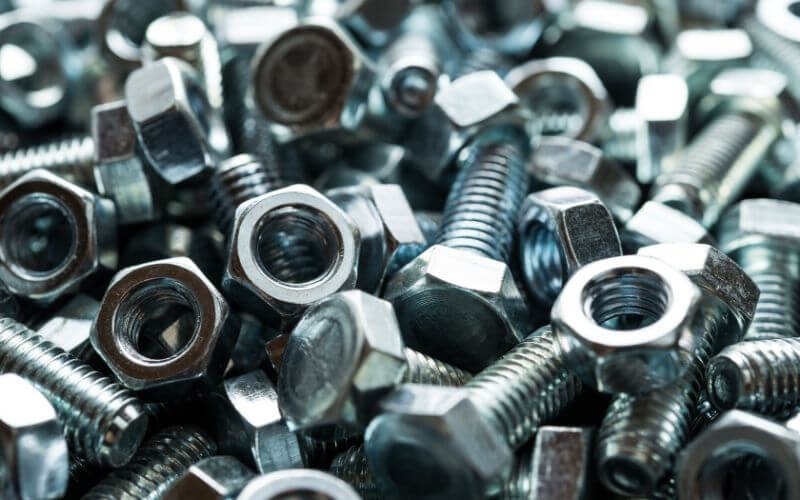
Phương pháp thứ tự thực thi (motion-step method)
Poka-yoke đảm bảo các bước thực thi được hoàn thành theo đúng quy định và thứ tự đã đề ra, hữu ích cho những công việc gồm nhiều hoạt động phối hợp lẫn nhau. Điểm khác biệt so với phương pháp giá trị cố định là cách thức này nhấn mạnh yếu tố trình tự. Từ đó, người phụ trách sẽ được cảnh báo nếu lỡ thực hiện không đúng hoặc bỏ qua một bước quy trình.
Nguồn gốc của Poka-Yoke
Ý tưởng về poka-yoke được lập ra bởi kỹ sư Shigeo Shingo (Nhật Bản), cũng là người phát triển nên một số công cụ và kỹ thuật quan trọng khác trong phạm vi sản xuất tinh gọn.
Năm 1961, Shingo đến thăm một cơ sở nhà máy với quy trình lắp ráp rất đơn giản nhưng vẫn để xảy ra tình trạng sản phẩm lỗi. Sau tìm hiểu, nguyên nhân chính là do nhân viên quên lắp lò xo vào một công tắc. Ban lãnh đạo đã phải cử một kỹ thuật viên đến mới có thể phát hiện ra lý do này, tiêu tốn khá nhiều thời gian và cả chi phí.
Từ đó, Shingo bắt đầu thiết kế các cách để chống sai sót cho hoạt động quy trình, đồng thời giúp mọi người ghi nhớ tốt hơn các công việc cần thiết để đảm bảo đúng tiêu chuẩn cần đạt, xuất phát bằng việc tạo danh sách checklist cho tác vụ hàng ngày.
Ban đầu, Shingo gọi cách thức phòng ngừa sai sót này là “baka-yoke”, tức “chống ngốc”. Nhưng điều này vô tình khiến người thực hiện trở thành đối tượng trọng tâm của nguyên nhân gây ra lỗi. Do vậy, sau này tên gọi đó đã được Shingo đổi thành “poka-yoke”, tức “chống lỗi”, vì mục tiêu chính là loại bỏ sai sót, chứ không phải để chỉ trích con người gây ra lỗi lầm đó.
Ví dụ ứng dụng của Poka Yoke trong sản xuất
Ngăn ngừa lỗi xử lý
Trong sản xuất, lỗi xử lý xảy ra khi quy trình được thực thi không chính xác – chẳng hạn như lắp ráp sai bộ phận, cài đặt bộ phận máy sai quy cách và trình tự…
Poka-yoke loại bỏ lỗi xử lý bằng cách thiết kế các hệ thống khiến những lỗi này không thể xảy ra (hoặc rất khó xảy ra). Biện pháp phổ biến là triển khai tiêu chuẩn an toàn cho các công đoạn nhạy cảm dễ xảy ra lỗi.
Ví dụ, trong dây chuyền lắp ráp, poka-yoke giảm lỗi bằng cách sử dụng phụ kiện đầu nối có hình dạng độc đáo, đảm bảo chỉ có các bộ phận nhất định mới có thể lắp chính xác vào khớp vị trí, giống cơ chế đồ chơi xếp hình nâng cao vậy. Ngoài ra, doanh nghiệp nay còn có hệ thống cảm biến để thông báo kết quả tương ứng, ngay lập tức nhắc nhở nhân sự vận hành nếu vị trí được ghi nhận không chính xác.
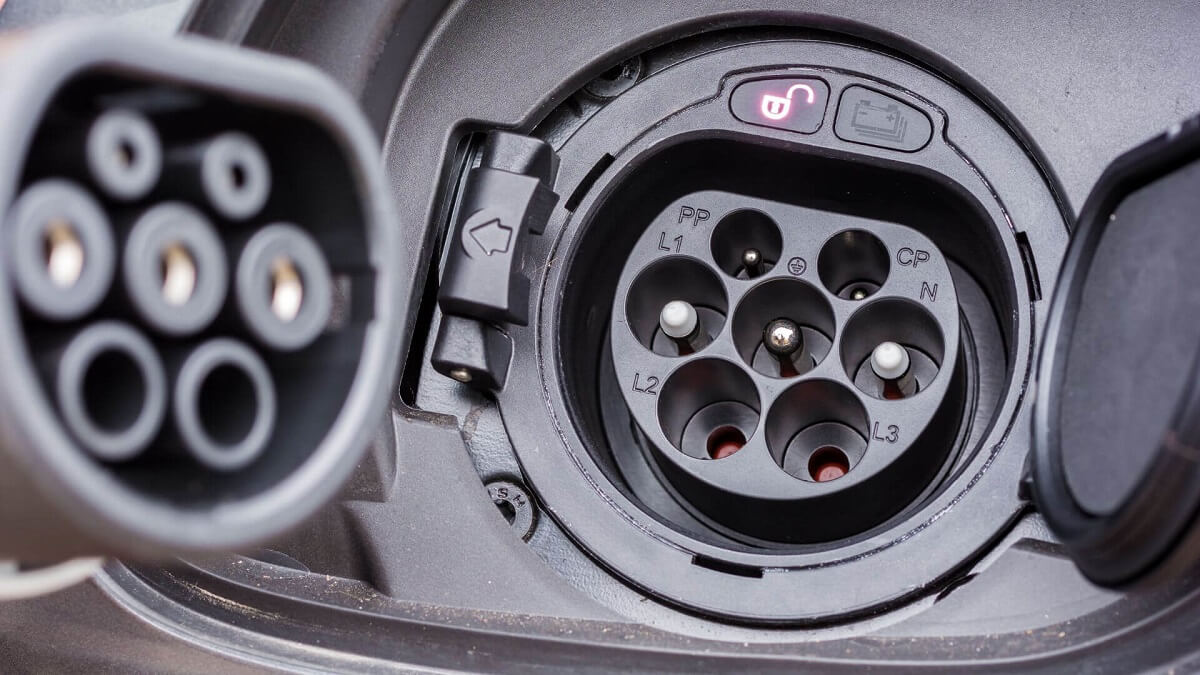
Ngăn ngừa lỗi thiết lập
Poka-yoke giúp ngăn ngừa lỗi liên quan đến quy trình cài đặt hoặc thiết lập trong nhà xưởng sản xuất, bằng cách triển khai các cơ chế chống lỗi thông qua mã màu, danh sách kiểm tra và cảm biến tự động. Những cách thức này giúp thiết bị được cấu hình chuẩn xác trước khi đi vào vận hành, nhằm giảm thời gian chết, phế phẩm và rủi ro gây hao tốn tài nguyên.
Ví dụ, mã màu công nghiệp thường được áp dụng cho dụng cụ, thiết bị và vật liệu để tối ưu tổ chức hoạt động. Các thùng đựng phụ tùng máy có màu đỏ sẽ tương ứng phụ kiện lỗi, xanh dành cho bộ phận đạt chuẩn. Từ đó, công nhân có thể ngay lập tức xác định nơi cần lấy đồ phù hợp, ngăn trường hợp nhầm lẫn khi lọc sản phẩm.
Ngăn ngừa lỗi thiếu linh kiện
Để loại bỏ rủi ro lỗi thiếu linh kiện, các doanh nghiệp thường áp dụng poka-yoke theo hình thức từng chặng cảm biến kiểm tra trên dây chuyền sản xuất. Những cảm biến này sẽ phát hiện sự hao hụt số lượng của thành phần bộ phận cần thiết. Nếu trường hợp đó xảy ra, hệ thống sẽ tự động dừng lại, báo hiệu cần khắc phục trước khi tiếp diễn quy trình.
Chẳng hạn, trên dây chuyền lắp ráp ô tô, những thành phần như bu-lông, ốc vít phải được kiểm kê nghiêm ngặt khi hoàn thiện máy móc. Khi bị thiếu phụ tùng, hệ thống sẽ không cho phép tiếp tục chạy mà chưa lắp đặt đủ hết các bộ phận như thiết lập tiêu chuẩn.
Ngăn ngừa lỗi sai linh kiện
Bối cảnh lắp phụ tùng và linh kiện sai cũng là vấn đề được giải quyết hiệu quả bởi poka-yoke. Cơ chế xử lý sai linh kiện cũng có nhiều điểm tương đồng với trường hợp khắc phục lỗi thiết lập, thông qua phương pháp phân loại theo mã màu hoặc thành phần kết nối có thiết kế độc nhất.
Ví dụ điển hình là thiết kế ren ốc vít xe đạp, chúng sẽ có chỉ số kỹ thuật về độ nghiêng khác nhau tương ứng với mỗi vị trí lắp trên xe. Cách làm này khiến ren cho bàn đạp bên trái và phải chỉ phù hợp để lắp đúng chính xác từng bên, không thể bị nhầm lẫn ngược lại.
Ngăn ngừa lỗi vận hành
Lỗi vận hành sẽ được kỹ thuật poka-yoke ngăn chặn nhờ các biện pháp cảnh báo tự động và nhắc nhở bằng tín hiệu trực quan, giúp nhân viên nhanh chóng phát hiện sai lệch so với quy trình tiêu chuẩn.
Các đèn LED báo hiệu trạng thái trên máy móc chính là ứng dụng phổ biến cho phương thức này. Đèn xanh cho biết hoạt động bình thường, trong khi đèn vàng báo hiệu các vấn đề nhỏ cần chú ý, và đèn đỏ dành cho vấn đề nghiêm trọng hoặc ngừng hoạt động.
Cơ chế phản hồi tức thì và dễ hiểu này cho phép nhân sự vận hành nhanh chóng xác định và giải quyết các vấn đề, giảm thời gian ngừng hoạt động, duy trì ổn định sản xuất cũng như tiêu chuẩn an toàn.
Ngăn ngừa lỗi đo lường
Những chỉ số và đại lượng cần thống kê chính xác (kích thức, khối lượng, nhiệt độ) để phục vụ công đoạn sản xuất cũng là mục tiêu ứng dụng poka yoke, nhằm giảm tỷ lệ lỗi kết quả đo lường.
Ví dụ, doanh nghiệp thường sử dụng các khuôn theo kích thước cố định đã được phê duyệt trước để làm mẫu cắt, lắp ráp, hoặc căn chỉnh thiết kế vật liệu. Cách tiếp cận này đảm bảo độ chính xác, giảm lãng phí tài nguyên và nâng cao tính nhất quán của sản phẩm cuối cùng.
5 bước triển khai áp dụng Poka-Yoke trong môi trường sản xuất
Bước 1: Xác định vấn đề gây lỗi
Bước đầu tiên để thực thi poka-yoke là xác định chính xác nơi xảy ra lỗi trong quy trình sản xuất, từ đó tạo tiền đề đào sâu về bản chất và nguyên nhân vấn đề. Một số phạm vi gợi ý có thể tham khảo như:
- Lỗi xuất phát từ trong quy trình sản xuất
- Lỗi thực thi bởi con người
- Lỗi bắt nguồn từ thiết kế sản phẩm
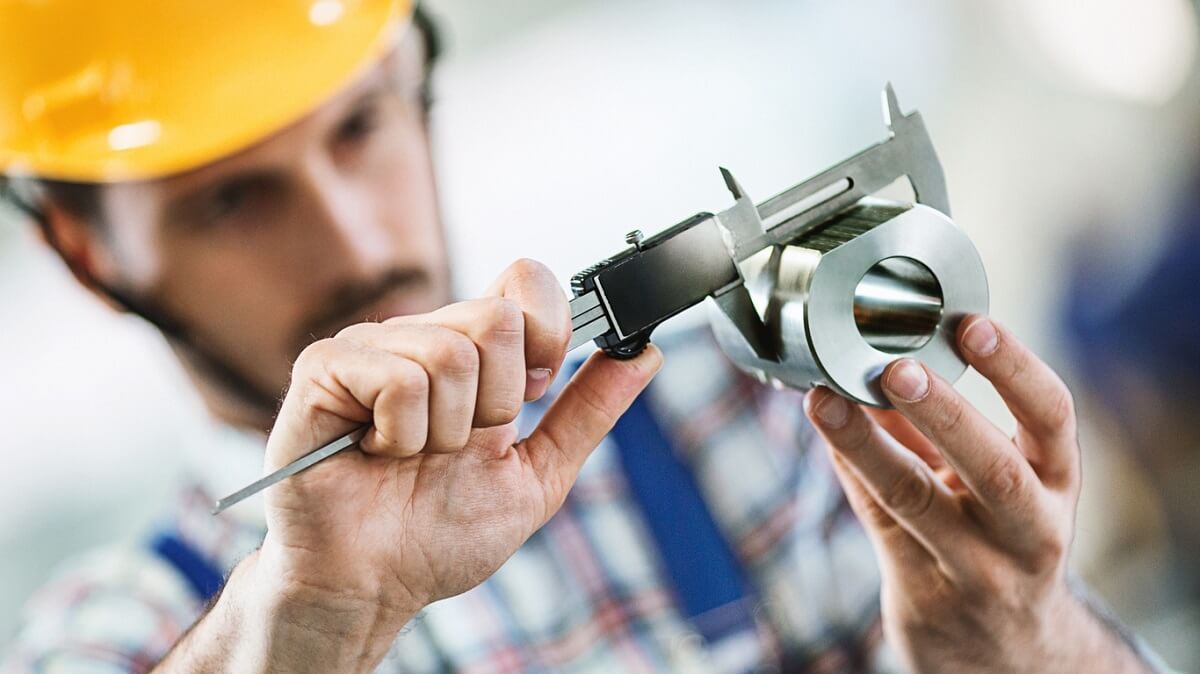
Bước 2: Xác định nguyên nhân gốc rễ của vấn đề
Sau khi xác định được yếu tố đại diện cho lỗi sai, giờ là lúc tìm hiểu nguyên nhân khiến vấn đề này xảy ra.
Có nhiều kỹ thuật phân tích nguyên nhân gốc rễ để áp dụng, trong đó một cách phổ biến nhất là phương pháp đặt “5 câu hỏi vì sao”.
Chẳng hạn, nếu một thiết bị trên dây chuyền sản xuất bị dừng đột ngột, hãy tìm lời giải đáp cho trình tự 5 câu hỏi sau:
- Vì sao máy dừng hoạt động? (do kẹt bánh răng)
- Vì sao bánh răng bị kẹt? (do cấu tạo lắp đặt máy không được căn chỉnh chuẩn xác)
- Vì sao cấu tạo máy lại bị lệch so với thiết kế gốc? (do tình trạng mài mòn tự nhiên trong quá trình vận hành lâu dài)
- Tại sao lỗi hao mòn vật liệu không được giải quyết sớm hơn? (do công tác quản lý bảo trì sản xuất không đủ cẩn thận)
- Tại sao nhóm kỹ thuật bảo trì bỏ sót vấn đề này? (do lịch kiểm tra máy không thường xuyên tập trung vào vị trí thiết lập đó)
Khi đã nắm rõ nguyên nhân gốc rễ, chúng ta sẽ tiến tới bước thiết lập phương pháp poka-yoke để ngăn chặn tái diễn tình trạng lỗi trên.
Bước 3: Xác định phương pháp poka-yoke phù hợp
Tại đây, cách giải quyết thường được chia thành 2 hướng:
- Nếu lỗi xảy ra có thể dễ dàng ngăn chặn: Hãy thiết lập một cơ chế poka-yoke có tác dụng tự động dừng quy trình ngay khi phát hiện lỗi, và chỉ cho phép tiếp tục sản xuất khi vấn đề đã sửa xong.
- Nếu lỗi xảy ra khó phát hiện kịp thời để sửa chữa: Hãy cài đặt phương thức poka-yoke có khả năng kiểm tra trạng thái hoạt động, đồng bộ tín hiệu cảnh báo theo màu sắc, đèn LED, chuông báo… hoặc bất kỳ hình thức nào giúp nhân viên nhận ra sự bất ổn định của tình trạng sản xuất.
Bước 4: Kiểm tra thử nghiệm hệ thống poka-yoke
Sau khi chọn cơ chế phù hợp để áp dụng poka-yoke, hãy tiến hành thử nghiệm hiệu quả của hệ thống trên quy mô nhỏ, theo hình thức thí điểm.
Lựa chọn phổ biến là một dây chuyền sản xuất hoặc máy độc lập, có thể kiểm soát toàn phần và giám sát chặt chẽ từng thay đổi trong trạng thái hoạt động, qua đó tinh chỉnh dần đặc tính giải pháp dựa trên kết quả thực tế.
Ngoài ra, doanh nghiệp cũng cần đảm bảo nhân sự liên quan nắm rõ về các bước thực thi xử lý, thu thập dữ liệu để báo cáo về sau.
Bước 5: Đào tạo nhân công và cập nhật quy trình chính thức
Sau khi hoàn thành một dự án thí điểm thành công, đã đến lúc triển khai đầy đủ hệ thống poka-yoke trong tổ chức doanh nghiệp. Đào tạo lực lượng lao động về phương pháp mới, có thể kết hợp nâng cao kỹ năng, tùy thuộc vào mức độ thay đổi cần cập nhật.
Khi hướng dẫn nhân sự, đừng quên đồng bộ thông tin liên quan từ phương pháp poka-yoke vào tài liệu và quy trình vận hành tiêu chuẩn hiện có, nhằm loại bỏ những xung đột và nhầm lẫn thông tin.
Tác dụng & lợi ích của Poka-Yoke
- Tiết kiệm thời gian đào tạo: Poka-yoke đơn giản hóa các quy trình, giúp chúng trở nên dễ hiểu và dễ thực hiện hơn, giảm đáng kể thời gian cần thiết để đào tạo nhân viên mới.
- Thúc đẩy văn hóa cải tiến liên tục: Bằng cách xác định và giải quyết lỗi tận gốc, poka-yoke khuyến khích công nhân không ngừng tìm cách cải tiến quy trình và chất lượng sản phẩm.
- Nâng cao an toàn: Với nhiều cơ chế phòng ngừa lỗi tốt hơn, poka-yoke giảm nguy cơ tai nạn và thương tích tại nơi làm việc.
- Giảm lãng phí: Giảm thiểu lỗi trong quá trình sản xuất dẫn đến ít công việc sửa chữa và phế phẩm hơn – giảm lãng phí và tiết kiệm tài nguyên.
- Tăng năng suất: Tối ưu hóa hoạt động và giảm thiểu lỗi tăng cường hiệu quả, cho phép sản lượng cao hơn trong thời gian ngắn hơn.
- Kiểm soát chất lượng tốt hơn: Poka-yoke đảm bảo sản phẩm đáp ứng tiêu chuẩn chất lượng một cách nhất quán, dẫn đến sự hài lòng cao hơn của khách hàng và chi phí thấp hơn liên quan đến lỗi.
Nhược điểm của Poka-Yoke
Giống như bất kỳ phương pháp cải tiến mới nào, poka-yoke cũng có thể có một số nhược điểm.
Một trong những vấn đề chính thường đến từ nhân sự: Họ có xu hướng không chịu làm quen với những thay đổi mới trong quy trình khi áp dụng phương pháp Poka-Yoke. Khi đó, doanh nghiệp cần có chiến lược tuyên truyền và cập nhật kiến thức đúng cách để tập thể nhận ra lợi ích chính đáng của thay đổi này. Đôi khi, công tác thích nghi có thể trở nên khó khăn nếu hiệu quả không được chứng minh rõ ràng sau khi áp dụng Poka-Yoke.