Digital Twin là gì? 5 ví dụ về Digital Twin trong sản xuất
Digital Twin (bản sao kỹ thuật số) là phiên bản ảo của một vật thể, người hoặc quy trình thực tế, được đặt trong một môi trường kỹ thuật số tương ứng. Digital Twin giúp các tổ chức mô phỏng các tình huống thực tế để tìm ra kết quả liên quan, bằng cách thực hiện các thử nghiệm, lập mô hình kịch bản, đào tạo nhân viên, và quan sát hoạt động của thiết bị trong các điều kiện khác nhau mà không cần phải vận hành thiết bị thực tế.
Nguyên lý hoạt động của Digital Twin
Giả sử đối tượng được chọn thử nghiệm là một tua-bin được trang bị nhiều cảm biến kết nối đến các chức năng quan trọng. Các cảm biến này giúp ghi nhận dữ liệu khác nhau về hiệu suất của đối tượng ngoài thực tế, như sản lượng năng lượng, nhiệt độ, điều kiện thời tiết… Hệ thống xử lý nhận thông tin này và áp dụng mô phỏng lên thực thể Digital Twin.
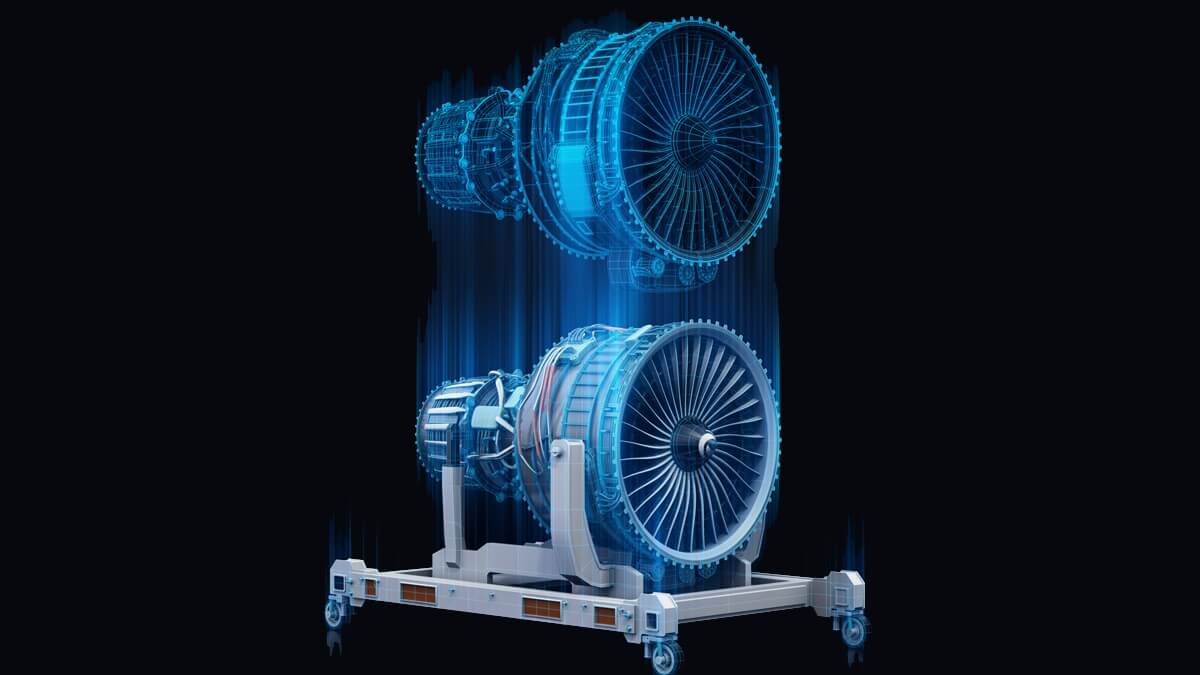
Sau khi tích hợp dữ liệu liên quan, Digital Twin sẽ được sử dụng để thực hiện các mô phỏng khác nhau, phân tích vấn đề về hiệu suất và đề xuất cải tiến khả thi. Mục tiêu cuối cùng là thu được kết quả phỏng đoán có tính chính xác cao, sau đó thống nhất áp dụng cho đối tượng thực tế ban đầu.
Sự khác biệt giữa Digital Twin & mô phỏng giả lập (simulation)
Mô phỏng giả lập và Digital Twin đều sử dụng mô hình kỹ thuật số để tái hiện lại bối cảnh. Tuy nhiên, Digital Twin lại sở hữu lợi thế vượt trội về môi trường ảo.
Điểm khác biệt lớn nhất nằm ở quy mô: Mô phỏng giả lập chỉ tập trung nghiên cứu một quy trình cụ thể, trong khi Digital Twin có thể hỗ trợ thực hiện đồng thời nhiều mô phỏng đa quy trình, mang lại bức tranh tổng thể chi tiết hơn về hệ thống.
Cụ thể, Digital Twin ghi điểm nhờ khả năng tiếp cận dữ liệu phong phú và cập nhật liên tục từ nhiều khía cạnh thông qua hệ thống cảm biến. Nhờ vậy, Digital Twin có thể mô phỏng chính xác và đánh giá hiệu quả hoạt động của hệ thống trong nhiều điều kiện khác nhau. Hơn nữa, môi trường ảo mạnh mẽ cung cấp sức mạnh tính toán vượt trội, giúp Digital Twin giải quyết các vấn đề phức tạp mà mô phỏng truyền thống khó có thể đáp ứng.
Với những ưu điểm trên, Digital Twin hứa hẹn mang đến tiềm năng to lớn trong việc cải thiện sản phẩm, tối ưu hóa quy trình và đưa ra quyết định sáng suốt hơn, góp phần thúc đẩy phát triển trong nhiều lĩnh vực.
Lợi ích của Digital Twin
Tối ưu kết quả nghiên cứu và phát triển
Digital Twin cho phép nghiên cứu và thiết kế sản phẩm hiệu quả hơn, tạo ra khối lượng lớn dữ liệu để phục vụ kết quả hiệu suất dự kiến. Thông tin đó có thể được tận dụng nhằm hoàn thiện và cải tiến sản phẩm trước cả khi bắt đầu sản xuất.
Tăng cường hiệu suất
Ngay khi một sản phẩm mới được đưa vào sản xuất, Digital Twin có thể tham gia vào mô phỏng và giám sát hệ thống, nhằm duy trì hiệu quả tối đa trong toàn bộ quá trình sản xuất.
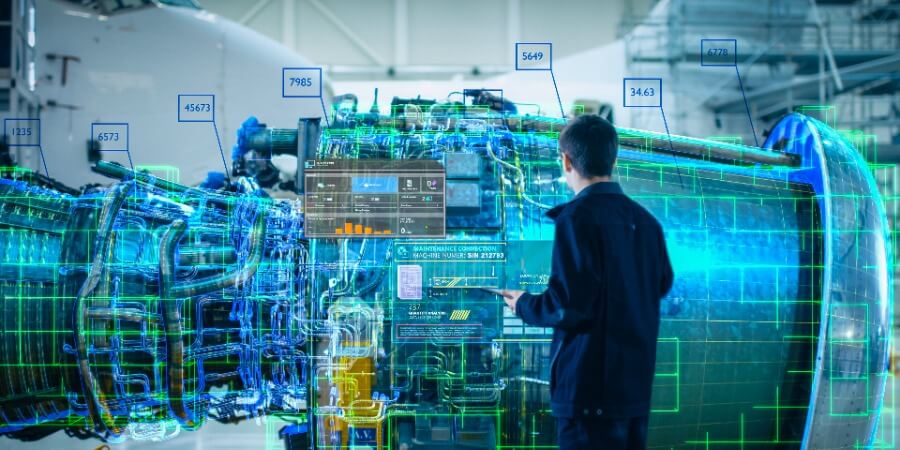
Dự trù phương án về vòng đời sản phẩm
Digital Twin thậm chí còn giúp các doanh nghiệp quyết định cách xử lý các sản phẩm đến hồi kết của vòng đời sản xuất, cần được xử lý thông qua tái chế hoặc các biện pháp khác. Nhờ Digital Twin, họ có thể xác định được vật liệu sản phẩm nào nên thu hồi, kết hợp với đề xuất khả thi nếu có.
Ứng dụng của Digital Twin
Digital Twin đang được ứng dụng rộng rãi trong các lĩnh vực sau:
- Thiết bị phát điện: Những loại hình động cơ quy mô lớn – như động cơ phản lực, động cơ xe lửa và tua-bin phát điện – hưởng lợi rất nhiều từ Digital Twin, đặc biệt là trong việc xác định khung thời gian bảo trì định kỳ.
- Cơ sở hạ tầng và hệ thống: Các công trình lớn như tòa nhà cao tầng hay giàn khoan ngoài khơi có thể được tối ưu nhờ ứng dụng Digital Twin trong quá trình thiết kế. Ngoài ra, công nghệ này còn hữu ích trong việc tạo dựng các hệ thống tiện ích nội bộ, như hệ thống sưởi, thông gió và điều hòa không khí (HVAC).
- Quy trình sản xuất: Vì Digital Twin được thiết kế để phản ánh toàn bộ vòng đời của sản phẩm, nên không có gì ngạc nhiên khi công nghệ này trở nên phổ biến trong tất cả các giai đoạn sản xuất, bao gồm định hướng sản phẩm từ thiết kế đến khi hoàn thiện và tất cả các bước trung gian.
- Dịch vụ y tế: Bệnh nhân sử dụng dịch vụ chăm sóc sức khỏe cũng thuộc nhóm hưởng lợi từ Digital Twin. Hệ thống dữ liệu tạo ra từ cảm biến có thể kết hợp với thông tin hồ sơ bệnh án cá nhân, nhằm theo dõi chỉ số sức khỏe và dự đoán triệu chứng hoặc phương pháp điều trị.
- Công nghiệp ô tô: Thiết kế ô tô yêu cầu tới nhiều loại hệ thống phức tạp được vận hành và đồng bộ trơn tru – một lý do rất thích hợp để ứng dụng công nghệ Digital Twin, vừa tăng hiệu quả sản xuất, vừa cải thiện chất lượng cuối.
- Quy hoạch đô thị: Nhân sự làm việc trong các dự án quy hoạch đô thị nói chung và kỹ sư xây dựng nói riêng đều nhận được rất nhiều lợi ích từ Digital Twin, hỗ trợ hiển thị dữ liệu không gian 3D và 4D thời gian thực, tích hợp được cả hệ thống thực tế tăng cường (AR) vào kế hoạch thi công.
5 ví dụ về ứng dụng Digital Twin trong sản xuất
Đào tạo nhân viên mới
- Thách thức: Tuyển dụng, đào tạo, đảm bảo nhân viên mới chủ động làm quen hiệu quả và an toàn với quy trình vận hành là một khoản đầu tư và chi phí lớn. Chọn phòng học riêng làm không gian đào tạo sẽ thiếu môi trường tiếp cận và minh họa thực tế, còn chọn không gian ngay tại nhà máy hoặc xưởng sản xuất lại bị ảnh hưởng tương tác do hoạt động sản xuất và tiếng ồn.
- Giải pháp: Digital Twin mô phỏng lại không gian nhà máy cho phép nhân viên mới khám phá và trải nghiệm môi trường làm việc một cách chân thật mà không lo ngại bất kỳ rủi ro vật lý hoặc gián đoạn sản xuất nào. Nhờ công nghệ này, họ có thể di chuyển tham quan trong môi trường làm việc ảo và hoàn thành các bài đào tạo AR để hiểu rõ hơn về môi trường thực tế nơi họ sẽ áp dụng kỹ năng của mình.
Tái cơ cấu không gian
- Thách thức: Số lượng máy móc tăng lên, quy trình làm việc thay đổi và những đề xuất vận hành khác sẽ dẫn đến nhu cầu tái sắp xếp không gian. Khi đó, việc lập kế hoạch thực thi bằng bản vẽ truyền thống có thể tăng tỉ lệ rủi ro và sai lệch thông tin.
- Giải pháp: Với hình ảnh đa chiều Digital Twin mô phỏng chính xác kích thước của cơ sở sản xuất, việc lập kế hoạch bố trí máy móc, xây dựng phân xưởng và tuân thủ các quy định đảm bảo một nơi làm việc an toàn trở nên dễ dàng hơn bao giờ hết. Các thành viên truy cập trình mô phỏng có thể hoạt động và tương tác cùng với nhau cùng lúc, thống kê lại bằng tài liệu để tổng hợp thông tin cần thiết trước khi đi đến thống nhất cuối cùng.
Bảo trì bảo dưỡng
- Thách thức: Không ai biết trước khi nào máy móc sẽ hỏng và trục trặc. Một sự cố bất ngờ yêu cầu sửa chữa gấp có thể cản trở quá trình sản xuất và ảnh hưởng tiêu cực đến doanh thu.
- Giải pháp: Liên kết thông tin sửa chữa, hướng dẫn sử dụng và các tài liệu cần thiết khác với từng vật thể mô phỏng trong Digital Twin giúp việc lập kế hoạch sửa chữa trở nên nhanh chóng và trực quan hơn. Nếu tích hợp thêm thiết bị kết nối IoT, Digital Twin có thể cung cấp thông tin bảo trì dự đoán ngoài ngữ cảnh vật lý – giúp doanh nghiệp đối phó sửa chữa kịp thời, hiệu quả.
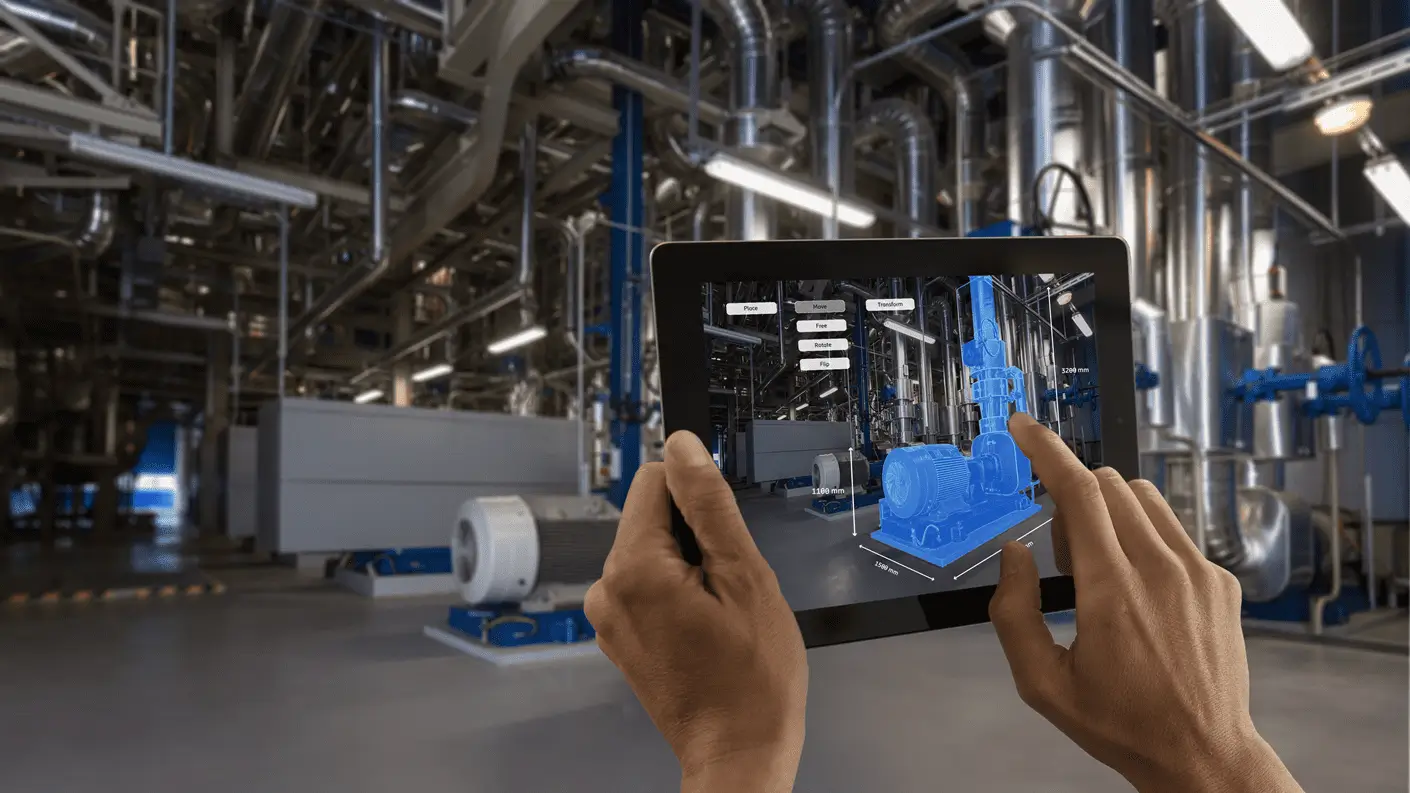
Kiểm định địa điểm từ xa
- Thách thức: Đối với các doanh nghiệp có nhiều cơ sở nhà máy ở nhiều địa điểm khác nhau, việc đảm bảo quy trình sản xuất được đồng bộ về cả chuyên môn và hiệu quả là nhiệm vụ tối quan trọng. Tuy nhiên, thực hiện điều đó một cách suôn sẻ thường yêu cầu giám sát trực tiếp, tốn nhiều thời gian và nguồn lực.
- Giải pháp: Gửi bản sao kỹ thuật số của một chi nhánh cho các bộ phậm phụ trách kiểm định. Thay vì phải đi công tác tốn kém, các cấp lãnh đạo chỉ cần sử dụng thiết bị di động để xem môi trường mô phỏng ảo của dây chuyền sản xuất và toàn bộ bối cảnh không gian xung quanh.
Đón tiếp khách hàng và đối tác
- Thách thức: Tương tự như bối cảnh đào tạo nhân viên mới, việc đón tiếp khách hàng và đối tác tới phân xưởng có khả năng cao bị gián đoạn do tiếng ồn, hoặc các sự cố an toàn không lường trước.
- Giải pháp: Với Digital Twin 3D, khách hàng và đối tác có thể trải nghiệm môi trường ảo trên bất kỳ thiết bị nào, bao gồm cả thực tế ảo (VR), mà không cần trực tiếp bước vào cơ sở.