7 lỗi sai thường gặp khi tích hợp OEE vào quy trình sản xuất
OEE sinh ra để trở thành cánh tay phải giúp doanh nghiệp đánh giá hiệu suất tổng thể, đồng thời tìm hướng khắc phục những vấn đề tồn đọng.
Tuy nhiên, nắm rõ cách tính toán OEE hay áp dụng OEE vào quy trình là chưa đủ. Lãnh đạo doanh nghiệp cần có góc nhìn đa chiều hơn, hiểu rõ những lỗi lầm thường gặp khiến dữ liệu OEE bị sai lệch, không bám sát thực tế.
Dưới đây là 7 lỗi sai phổ biến mà doanh nghiệp thường mắc phải khi tích hợp OEE trong hoạt động quản lý sản xuất, kèm theo đề xuất phương án khắc phục hiệu quả.
Lỗi sai 1: So sánh OEE của các quy trình khác nhau
Đối chiếu điểm số OEE của nhiều máy móc trong cùng một quy trình hoặc dây chuyền sản xuất thì không có gì đáng bàn cãi. Tuy nhiên, điều tương tự không nên được áp dụng giữa các bộ phận sản xuất mang tính chất khác nhau, hoặc có cách vận hành độc lập. Hành động này sẽ không đem lại kết quả tốt đẹp, thậm chí có thể khiến quyết định đưa ra trở nên lệch lạc so với định hướng ban đầu.
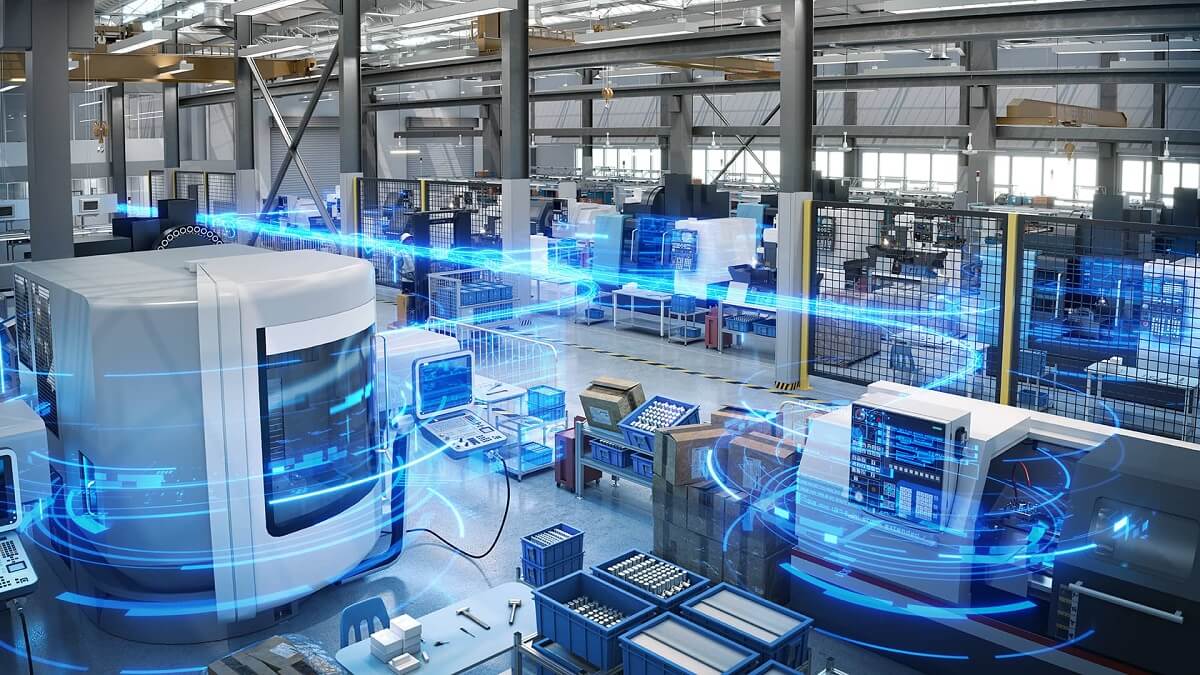
Chẳng hạn, giữa một thiết bị có cơ chế yêu cầu 5 lần chuyển giao chu kỳ sản xuất/ngày so với thiết bị chỉ cần 1 lần chuyển giao chu kỳ sản xuất/ngày, việc so sánh số liệu của cả 2 sẽ chẳng giúp ích gì về tính thực tiễn. Rõ ràng, thiết bị có 1 lần chuyển giao chu kỳ sẽ thể hiện tính khả dụng (availability) cao hơn, nhưng điều này không hẳn phản ánh hiệu quả tốt, vẫn cần thêm dữ liệu để kết luận.
Do vậy, trước khi đánh giá OEE, doanh nghiệp cần phân loại rõ ràng các nhóm thiết bị có chung cơ chế và tính chất hoạt động. Từ đó, mỗi nhóm sẽ được đối chiếu giữa trên thang điểm liên quan đặc thù, để rút ra kết quả sát sao nhất theo thực tế.
Lỗi sai 2: Tính OEE cho toàn bộ hệ thống quy trình sản xuất
Mặc dù khái niệm OEE “hiệu suất thiết bị tổng thể”, nhưng không có nghĩa doanh nghiệp nên tính điểm OEE cho tổng thể toàn bộ hệ thống. Kết quả nhận được có thể một phần phản ánh tình trạng vận hành sản xuất chung, nhưng cũng không thể nói lên những vấn đề gốc rễ chuyên sâu.
Cách làm được khuyến nghị là phân chia quy trình tính điểm OEE theo từng theo từng dây chuyền hoặc nhóm thiết bị cụ thể. Lựa chọn này sẽ đảm bảo doanh nghiệp dễ dàng xác định tận gốc những nhược điểm tồn tại để khắc phục đúng hướng, không bị đánh đồng theo kết quả đại diện cho một nhóm thiết bị quá lớn nhưng có khả năng sai lệch.
Lỗi sai 3: Ghi nhận dữ liệu OEE theo thời hạn quá ngắn
Quá trình theo dõi và cập nhật số liệu thiết bị nhằm phục vụ phân tích OEE nên diễn ra theo thời hạn đủ dài, giúp hạn chế tính chất kết quả nhất thời, không bám sát thực tế.
Nếu tính OEE chỉ trên thời gian hoạt động tương ứng một ngày hoặc một phiên sản xuất, dữ liệu thu thập có thể dẫn tới những kết luận mơ hồ, thiếu chính xác. Mặt khác, thời lượng khoảng 1 tháng thường tối ưu hơn cả, thống kê được toàn bộ các xu hướng thăng trầm về diễn biến hiệu suất hay thời gian chết.
Lỗi sai 4: Không giới thiệu hệ thống cho nhân sự
Đội ngũ nhân công trong doanh nghiệp sản xuất đóng vai trò rất quan trọng, bởi họ chịu trách nhiệm cho mọi công việc vận hành dây chuyền hàng ngày. Bất kể nhân viên hay trưởng bộ phận, tất cả cần được phổ biến kỹ càng về những đổi mới sắp tới trong hệ thống – cụ thể là việc tích hợp OEE vào quản lý sản xuất.
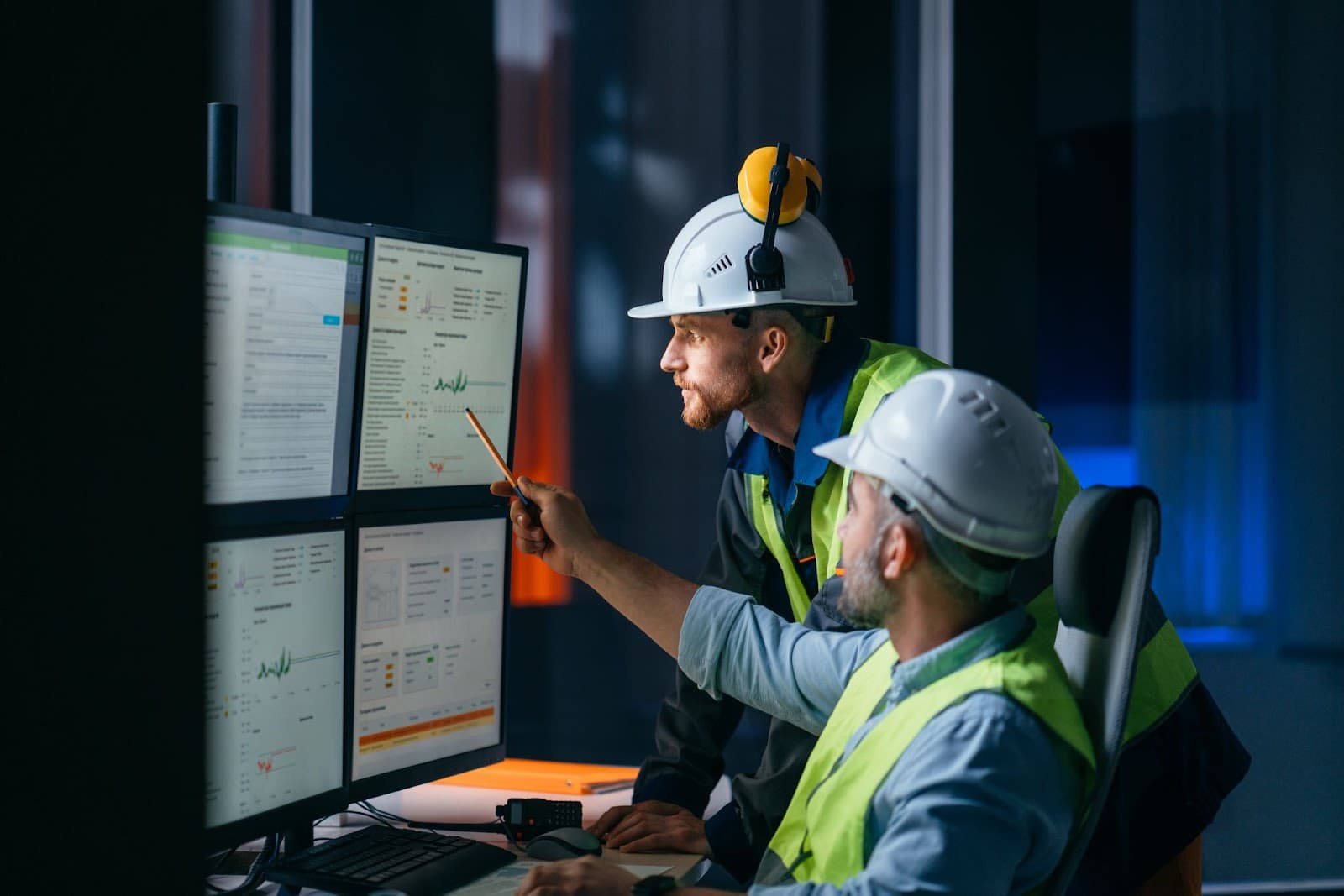
Trên hết, họ là những người hiểu rõ nhất cách phân tích và diễn giải dữ liệu OEE, rút ra kết luận từ những chỉ số thất thoát tài nguyên để cải tiến hiệu quả. Hơn nữa, nếu không lên kế hoạch phổ biến thông tin kỹ càng trong nội bộ đội nhóm, nhiều khả năng tinh thần tiếp thu sẽ đi xuống, khiến giai đoạn áp dụng OEE không có một khởi đầu suôn sẻ như kỳ vọng.
Lỗi sai 5: Ưu tiên số liệu trung bình về thời gian chu kỳ sản xuất
Khi tính toán thời gian hoàn thành chu kỳ sản xuất, doanh nghiệp cần ghi nhận số liệu lý tưởng, tức thời gian hoàn thành chu kỳ sản xuất nhanh nhất, thay vì chọn con số trung bình.
Trường hợp tính trung bình dường như là con số phản ánh tổng quan hơn, nhưng sự thực không phải như vậy. Trái lại, kết quả đó sẽ che khuất những yếu tố lẽ ra phải được vạch trần càng cụ thể càng tốt, như chênh lệch về thời gian bị thất thoát hoặc các sự cố đình trệ sản xuất. Sau cùng, điểm số OEE của doanh nghiệp sẽ tăng lên nếu tính thời gian trung bình, nhưng tất cả chỉ là một bức màn số liệu không xác đáng.
Mặt khác, việc tính toán thời gian lý tưởng hoàn thành chu kỳ sản xuất sẽ biến nó trở thành ngưỡng tiêu chuẩn bền vững, có thể dùng so sánh với hiệu quả quy trình thực tế trong mọi trường hợp, thỏa mãn điều kiện phân tích OEE.
Lỗi sai 6: Thu thập dữ liệu thủ công
Tổng hợp dữ liệu OEE bằng tay không phải là bất khả thi, nhưng sẽ hứng chịu rất nhiều rủi ro sai sót, chưa kể lãng phí thời gian và nhân lực. Hơn nữa, các quy trình sản xuất ngày một trở nên phức tạp và hiện đại hơn, nên phương pháp thủ công sẽ dần bộc lộ nhược điểm ngày một rõ.
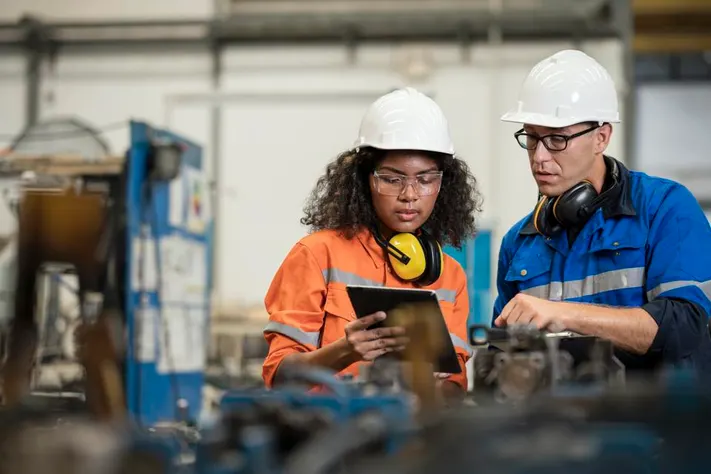
Đó là lý do các giải pháp phần mềm và hệ thống tự động thu thập dữ liệu OEE ra đời, chứng minh được ưu thế nổi bật về độ chính xác, tối ưu thời gian, giảm thiểu lãng phí tài nguyên, chi phí và nguồn lực nhân công, thậm chí còn dễ dàng nhân rộng quy mô theo lộ tình phát triển doanh nghiệp.
Lỗi sai 7: Chưa hiểu rõ ý nghĩa số liệu OEE
Chỉ số OEE chắc chắn phản ánh tình trạng hoạt động của hệ thống máy móc, đúng nhưng chưa đủ, vì lãnh đạo doanh nghiệp có thể tận dụng nó tốt hơn. Mục đích ẩn giấu phía sau OEE chính là khả năng xác định điểm yếu trong quy trình sản xuất, từ đó lên kế hoạch giải quyết triệt để. Nếu hiểu và làm được điều đó, tự khắc điểm OEE sẽ dần được cải thiện.
Tiếc thay, không ít quản lý vẫn còn tập trung quá nhiều vào bề nổi, chỉ chú ý đến những gì doanh nghiệp đạt được thông qua OEE, mà quên mất những gì doanh nghiệp đang bỏ sót. Chính những hành động và quyết định đưa ra dựa trên cơ sở điểm OEE mới nên là ưu tiên hàng đầu, giúp doanh nghiệp phát triển và giữ vững vị thế trên thị trường.
ĐỌC THÊM: