Lời giải cho ngành phụ tùng ô-tô Việt Nam trước trở ngại thuế quan mới từ Mỹ
Hiện nay, các doanh nghiệp sản xuất ô tô và phụ tùng Việt Nam đang phải đối diện với một thực tế kinh tế đầy thử thách. Chính sách “thuế quan đối ứng” với mức áp đặt 46% từ Hoa Kỳ đã và đang tạo ra những áp lực nặng nề đối với các nhà xuất khẩu Việt Nam, dẫn đến tình trạng chi phí gia tăng đáng kể và khả năng cạnh tranh suy giảm trên thị trường Mỹ.
Trong bối cảnh ấy, nhu cầu kiểm soát chi phí và nâng cao hiệu quả sản xuất trở nên cấp thiết hơn bao giờ hết. Các doanh nghiệp sản xuất buộc phải tìm ra những phương án tối ưu nhằm bù đắp chi phí phát sinh do thuế quan, đồng thời vẫn phải đảm bảo duy trì chất lượng sản phẩm và tiến độ giao hàng. Có thể nói, áp lực tối ưu hóa quy trình hoạt động chưa từng lớn đến vậy.
Vai Trò Thiết Yếu Của Quản Lý Chất Lượng Trong Giai Đoạn Áp Lực Kinh Tế
Trong bối cảnh phải đối mặt với những áp lực kinh tế từ bên ngoài như thuế quan, công tác quản lý chất lượng ngày càng khẳng định vai trò chiến lược. Chất lượng không đảm bảo sẽ tạo ra những chi phí tiềm ẩn, vốn có thể làm suy giảm thêm biên lợi nhuận vốn đã mỏng manh:
- Các lô hàng bị từ chối, dẫn đến phát sinh chi phí chế tạo lại hoặc thay thế
- Hàng hóa bị khách hàng hoàn trả, làm phát sinh thêm chi phí hậu cần
- Phát sinh chi phí bảo hành và sửa chữa liên quan
- Uy tín thương hiệu bị tổn hại, dẫn đến mất cơ hội kinh doanh
- Gia tăng yêu cầu về kiểm tra và thử nghiệm sản phẩm
Đối với ngành sản xuất phụ tùng ô tô, chất lượng là yếu tố không thể thỏa hiệp. Các bộ phận an toàn của xe cần phải đáp ứng những tiêu chuẩn nghiêm ngặt, các chi tiết cơ khí chính xác phải đạt được dung sai theo quy định. Một sai sót về chất lượng không đơn thuần chỉ dẫn đến việc một bộ phận bị loại bỏ, mà còn có thể khiến doanh nghiệp mất đi vị thế nhà cung cấp cho các tập đoàn sản xuất ô tô hàng đầu.
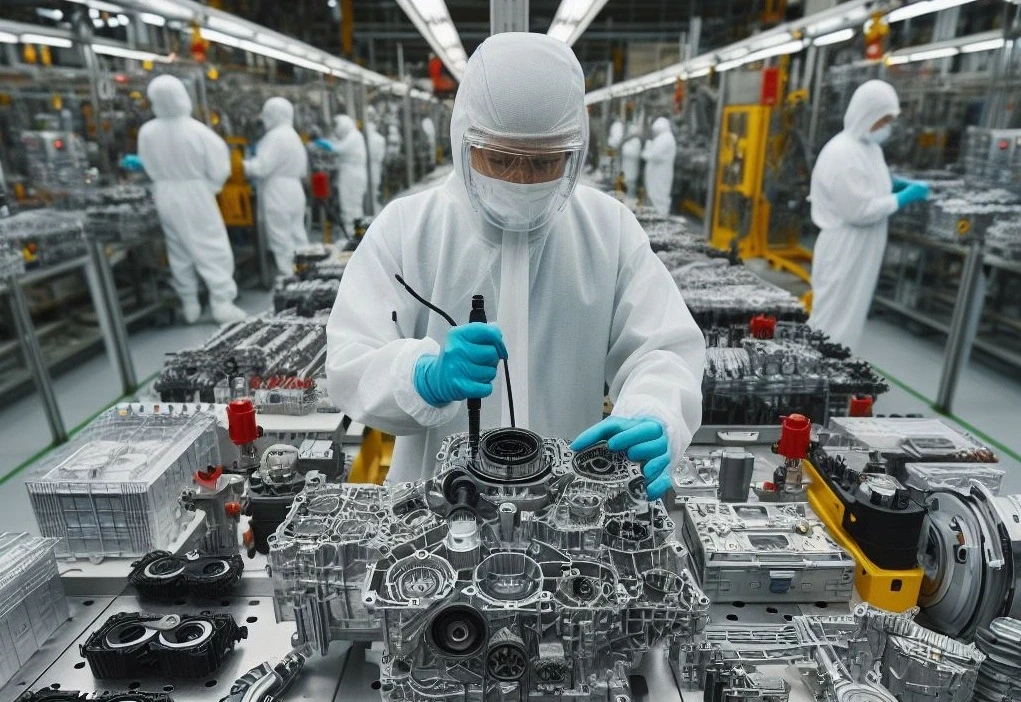
DxQMS: Giải Pháp Tối Ưu Chi Phí và Nâng Cao Hiệu Quả
Trong hệ sinh thái các giải pháp DxFAC, Hệ thống Quản lý Chất lượng (DxQMS) nổi bật như một công cụ mang lại những lợi ích thiết thực cho các doanh nghiệp sản xuất phụ tùng ô tô đang phải đối mặt với áp lực thuế quan.
DxQMS chuyển hóa công tác quản lý chất lượng từ quy trình kiểm tra thụ động sang hệ thống chủ động và phòng ngừa, giúp giảm thiểu lãng phí, hạn chế tối đa việc làm lại và ngăn chặn các lỗi chất lượng tốn kém. Phương pháp tiếp cận toàn diện này trực tiếp giải quyết áp lực chi phí phát sinh do chính sách thuế quan mới.
1. Giảm Thiểu Phế Phẩm và Chi Phí Tái Chế
Trong sản xuất, mỗi sản phẩm lỗi phát sinh đều là nguồn chi phí thuần túy. Mỗi chi tiết bị loại bỏ đồng nghĩa với việc lãng phí nguyên vật liệu, nhân công, thời gian vận hành máy móc và năng lượng. Tương tự, việc làm lại sản phẩm không chỉ làm tăng chi phí nhân công mà còn gây chậm trễ cho toàn bộ tiến độ sản xuất.
DxQMS khắc phục những vấn đề trên thông qua các phương thức sau:
- Thiết lập hệ thống kiểm tra chất lượng theo thời gian thực, phát hiện sớm vấn đề ngay trong quá trình sản xuất
- Áp dụng kiểm soát quy trình thống kê nhằm nhận diện các xu hướng tiềm ẩn trước khi chúng gây ra lỗi
- Xây dựng tài liệu minh bạch về yêu cầu chất lượng, tránh mọi nhầm lẫn có thể xảy ra
- Triển khai công cụ phân tích nguyên nhân gốc rễ, từ đó khắc phục triệt để các vấn đề tái diễn
- Phát triển hướng dẫn công việc chi tiết, giúp giảm thiểu lỗi vận hành
Giá Trị Thực Tiễn: Các doanh nghiệp sản xuất phụ tùng ô tô thường ghi nhận mức giảm 25-35% về phế phẩm và chi phí làm lại sau khi triển khai DxQMS, qua đó trực tiếp cải thiện biên lợi nhuận và giảm nhẹ tác động từ thuế quan.
2. Phòng Ngừa Tình Trạng Lô Hàng Bị Từ Chối
Khi một lô hàng không vượt qua được khâu kiểm tra của khách hàng, chi phí phát sinh thường tăng theo cấp số nhân:
- Chi phí vận chuyển hàng trả về
- Chi phí sản xuất gấp rút để thay thế sản phẩm bị từ chối
- Chi phí vận chuyển nhanh cho các đơn hàng thay thế
- Chi phí hành chính liên quan đến việc xử lý hàng bị từ chối
- Tổn hại về mối quan hệ với khách hàng
DxQMS ngăn chặn những tình huống này thông qua:
- Quy trình xác minh kỹ lưỡng trước khi giao hàng
- Hệ thống thu thập dữ liệu kiểm tra tự động hóa
- Xây dựng tiêu chí nghiệm thu rõ ràng cho từng sản phẩm
- Số hóa quy trình chứng nhận và tài liệu kỹ thuật
- Đảm bảo khả năng truy xuất nguồn gốc xuyên suốt quá trình sản xuất
Giá Trị Thực Tiễn: Các nhà sản xuất thường chứng kiến tỷ lệ lô hàng bị từ chối giảm 40-60% sau khi triển khai hệ thống quản lý chất lượng toàn diện, qua đó giảm đáng kể những chi phí phát sinh có tác động cao.
3. Tối Ưu Hóa Quy Trình Tuân Thủ và Chứng Nhận
Các doanh nghiệp sản xuất phụ tùng ô tô buộc phải tuân thủ nhiều tiêu chuẩn và quy định khắt khe như IATF 16949, ISO 9001, cùng các yêu cầu đặc thù từ phía khách hàng. Việc quản lý tuân thủ theo phương pháp thủ công không chỉ tốn kém nhân lực mà còn tiềm ẩn nhiều rủi ro sai sót.
DxQMS hỗ trợ công tác tuân thủ thông qua:
- Hệ thống quản lý tài liệu tập trung cho các tiêu chuẩn và quy trình
- Tự động hóa việc lập lịch và theo dõi kiểm toán
- Tích hợp trực tiếp các yêu cầu vào hướng dẫn công việc
- Quản lý số hóa các biện pháp khắc phục và phòng ngừa
- Đảm bảo khả năng truy xuất nguồn gốc toàn diện phục vụ yêu cầu pháp lý
Giá Trị Thực Tiễn: Các nhà sản xuất thường cắt giảm được 30-40% chi phí quản lý tuân thủ, đồng thời nâng cao chất lượng kết quả kiểm toán.
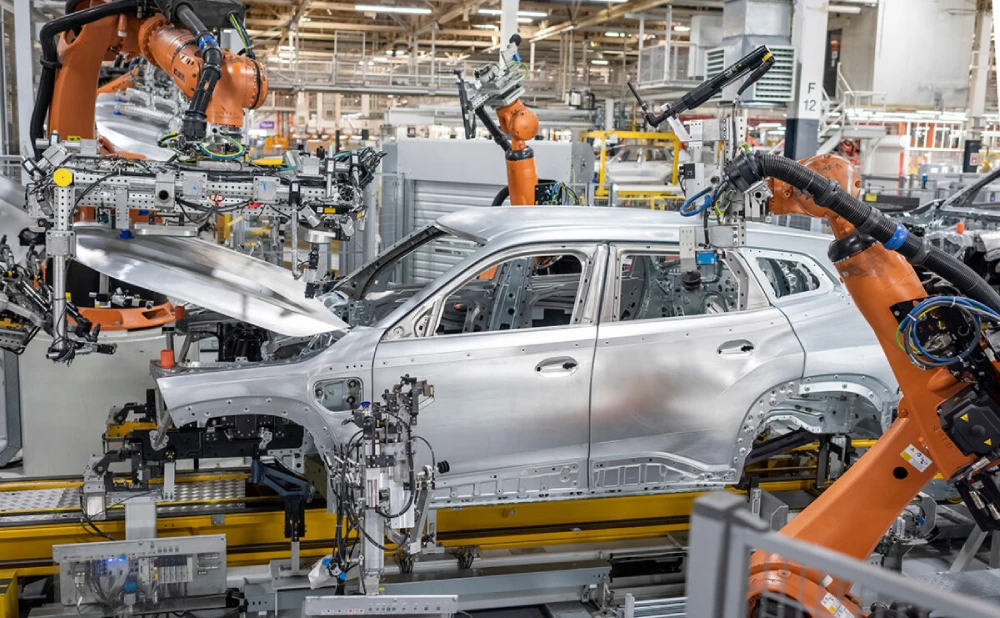
4. Nâng Cao Chất Lượng Ngay Từ Lần Đầu Tiên
Đạt được chất lượng ngay từ lần đầu tiên chính là phương thức tiết kiệm chi phí hiệu quả nhất trong sản xuất. Mỗi sai sót chất lượng đều làm phát sinh thêm chi phí, ảnh hưởng trực tiếp đến biên lợi nhuận.
DxQMS nâng cao chất lượng lần đầu thông qua:
- Xây dựng tiêu chuẩn chất lượng minh bạch, dễ tiếp cận đối với mọi nhân viên
- Thiết lập hệ thống phản hồi theo thời gian thực về quy trình sản xuất
- Áp dụng quy trình chống lỗi (poka-yoke)
- Triển khai hệ thống xác minh đào tạo cho người vận hành
- Phát triển kế hoạch kiểm soát cho các đặc tính quan trọng
Giá Trị Thực Tiễn: Các nhà sản xuất thường ghi nhận tỷ lệ chất lượng lần đầu cải thiện 15-25% sau khi triển khai DxQMS, trực tiếp nâng cao năng suất và biên lợi nhuận.
5. Tăng Cường Quản Lý Chất Lượng Nhà Cung Cấp
Các doanh nghiệp sản xuất phụ tùng ô tô thường phụ thuộc vào hệ thống nhà cung cấp để cung ứng linh kiện hoặc nguyên vật liệu đầu vào. Chất lượng đầu vào không đảm bảo sẽ gây ra hàng loạt vấn đề trong toàn bộ chuỗi sản xuất.
DxQMS giải quyết thách thức này thông qua:
- Triển khai hệ thống theo dõi chất lượng và bảng điểm đánh giá nhà cung cấp
- Xây dựng thông số kỹ thuật rõ ràng cho các mặt hàng mua vào
- Thiết lập quy trình kiểm tra đầu vào và thu thập dữ liệu
- Quản lý yêu cầu hành động khắc phục đối với nhà cung cấp
- Áp dụng cơ chế quản lý nhà cung cấp dựa trên hiệu suất
Giá Trị Thực Tiễn: Các nhà sản xuất thường chứng kiến lỗi chất lượng đầu vào giảm 30-40%, qua đó giảm thiểu gián đoạn sản xuất và chi phí liên quan.
Thành Công Của Doanh Nghiệp Sản Xuất Việt Nam Với DxQMS
Một doanh nghiệp sản xuất hàng đầu tại Việt Nam, từng đối mặt với áp lực cạnh tranh tương tự như những thách thức do chính sách thuế quan mới tạo ra, đã triển khai thành công hệ thống DxQMS nhằm chuyển đổi toàn diện phương pháp quản lý chất lượng. Hành trình của doanh nghiệp này chính là minh chứng thuyết phục cho hiệu quả của hệ thống.
Thực Trạng Ban Đầu
Trước khi áp dụng DxQMS, doanh nghiệp này đối diện với những khó khăn:
- Tỷ lệ phế phẩm cao ngất ngưởng ở mức 8-10%
- Tỷ lệ lô hàng bị từ chối trung bình lên đến 7% tổng sản lượng
- Công tác quản lý tuân thủ đòi hỏi 3 nhân viên làm việc toàn thời gian
- Tỷ lệ chất lượng lần đầu chỉ đạt 82%, thấp hơn tiêu chuẩn ngành
- Vấn đề chất lượng từ nhà cung cấp ảnh hưởng tới 15% nguyên vật liệu đầu vào
Lộ Trình Triển Khai
Doanh nghiệp này đã theo đuổi chiến lược triển khai theo từng giai đoạn:
Giai đoạn 1 (2 tháng đầu tiên):
- Triển khai hệ thống DxQMS cho những dây chuyền sản phẩm có tỷ lệ từ chối cao nhất
- Thiết lập hệ thống thu thập dữ liệu chất lượng số hóa
- Xây dựng hướng dẫn công việc chuẩn hóa cho các hoạt động trọng yếu
- Khởi động quy trình theo dõi chi phí chất lượng và tỷ lệ lỗi
Giai đoạn 2 (Tháng 2-4):
- Mở rộng phạm vi áp dụng hệ thống tới toàn bộ dây chuyền sản xuất
- Triển khai hệ thống kiểm soát quy trình thống kê cho các thông số then chốt
- Phát triển quy trình hành động khắc phục bài bản
- Thiết lập cơ chế quản lý chất lượng nhà cung cấp
- Tích hợp dữ liệu chất lượng với hệ thống sản xuất
Giai đoạn 3 (Tháng 4-6):
- Triển khai công nghệ phân tích chất lượng dự báo
- Phát triển quy trình lập kế hoạch chất lượng nâng cao
- Tích hợp trực tiếp với hệ thống quản lý chất lượng của khách hàng chủ chốt
- Xây dựng hệ thống phân tích chi phí chất lượng toàn diện
- Điều chỉnh hệ thống quản lý chất lượng theo các tiêu chuẩn quốc tế
Thành Quả Đạt Được
Sau quá trình triển khai toàn diện, doanh nghiệp này đã ghi nhận những thành tựu đáng kể:
1. Kiểm Soát Phế Phẩm và Chi Phí Tái Chế:
- Tỷ lệ phế phẩm giảm từ 8-10% xuống còn 5,2% (cải thiện 35%)
- Giờ công làm lại giảm 42%
- Tiết kiệm nguyên vật liệu hàng năm lên tới 420 triệu đồng
2. Khắc Phục Tình Trạng Lô Hàng Bị Từ Chối:
- Tỷ lệ lô hàng bị từ chối giảm từ 7% xuống còn 3,1% (giảm 56%)
- Loại bỏ hoàn toàn chi phí vận chuyển khẩn cấp cho hàng thay thế
- Số lượng khiếu nại từ khách hàng giảm 47%
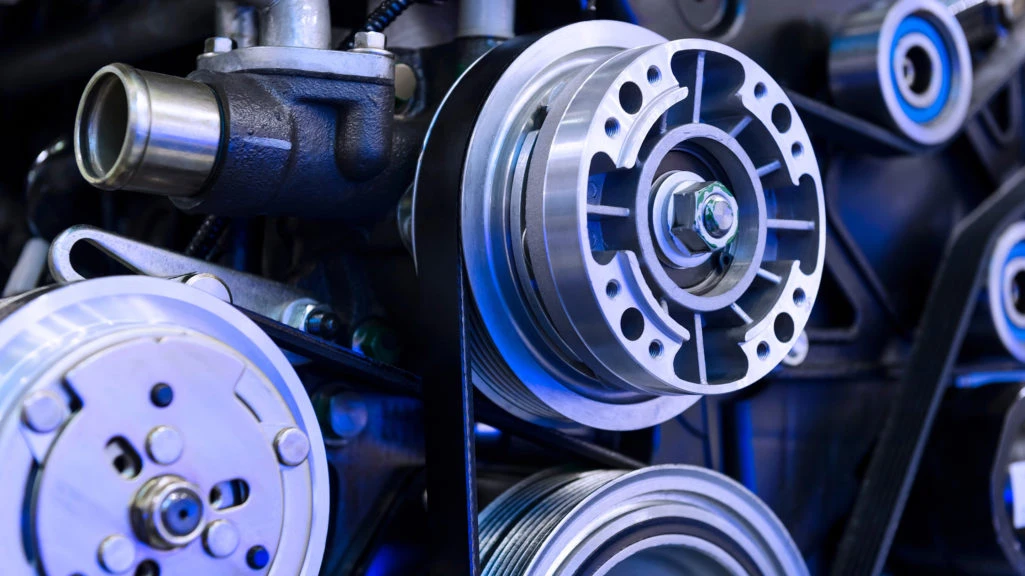
3. Tối Ưu Công Tác Tuân Thủ:
- Nguồn lực quản lý tuân thủ giảm từ 3 nhân viên toàn thời gian xuống còn 1,5
- Các phát hiện trong quá trình kiểm toán giảm 68%
- Thời gian tìm kiếm tài liệu giảm 75%
4. Nâng Cao Chất Lượng Lần Đầu:
- Tỷ lệ chất lượng lần đầu cải thiện từ 82% lên 96% (tăng 17%)
- Năng suất sản xuất tăng 12% với cùng nguồn lực
- Thời gian ngừng máy liên quan đến vấn đề chất lượng giảm 28%
5. Cải Thiện Chất Lượng Nhà Cung Cấp:
- Tỷ lệ lỗi chất lượng đầu vào giảm từ 15% xuống còn 9% (cải thiện 40%)
- Các gián đoạn sản xuất do nhà cung cấp giảm 62%
- Tối ưu hóa nguồn lực kiểm tra đầu vào, giảm 25%
Hiệu Quả Doanh Thu
Khía cạnh thuyết phục nhất trong quá trình triển khai DxQMS tại doanh nghiệp này chính là hiệu quả tài chính:
- Tổng chi phí đầu tư: 1,2 tỷ đồng
- Tiết kiệm năm đầu tiên: 3,8 tỷ đồng
- Hoàn vốn đầu tư trong vòng chưa đầy 4 tháng
- Mức tiết kiệm hàng năm liên tục: trên 4,2 tỷ đồng
Những kết quả định lượng này minh chứng rõ nét rằng DxQMS có thể mang lại hiệu quả giảm chi phí đáng kể – chính xác là điều mà các doanh nghiệp sản xuất phụ tùng ô tô đang cần để đối phó với tác động của mức thuế quan 46%. Chiến lược triển khai theo từng giai đoạn đã tạo ra những thành công nhanh chóng trong khi vẫn đảm bảo xây dựng nền tảng vững chắc hướng tới chuyển đổi chất lượng toàn diện, giúp doanh nghiệp nhận thấy lợi ích chỉ sau vài tuần triển khai.
Kết Luận
Mức thuế quan 46% từ Hoa Kỳ đặt ra thách thức không nhỏ đối với các doanh nghiệp sản xuất phụ tùng ô tô Việt Nam. Tuy nhiên, thông qua việc chuyển đổi công tác quản lý chất lượng từ một trung tâm chi phí thành lợi thế cạnh tranh chiến lược, các nhà sản xuất hoàn toàn có thể giảm nhẹ tác động này thông qua việc nâng cao hiệu quả nội bộ.
DxQMS mở ra con đường ngắn nhất dẫn đến những cải tiến toàn diện, đồng thời tác động tích cực đến nhiều trung tâm chi phí, từ đó hỗ trợ nâng cao sự hài lòng của khách hàng và củng cố uy tín thương hiệu. Trong bối cảnh áp lực từ bên ngoài gia tăng, việc tập trung vào nâng cao hiệu quả nội bộ càng trở nên quan trọng hơn bao giờ hết. DxQMS chính là công cụ mang lại sự tập trung đó, biến những thách thức tiềm ẩn thành cơ hội cải tiến hoạt động và nâng tầm chất lượng sản phẩm.